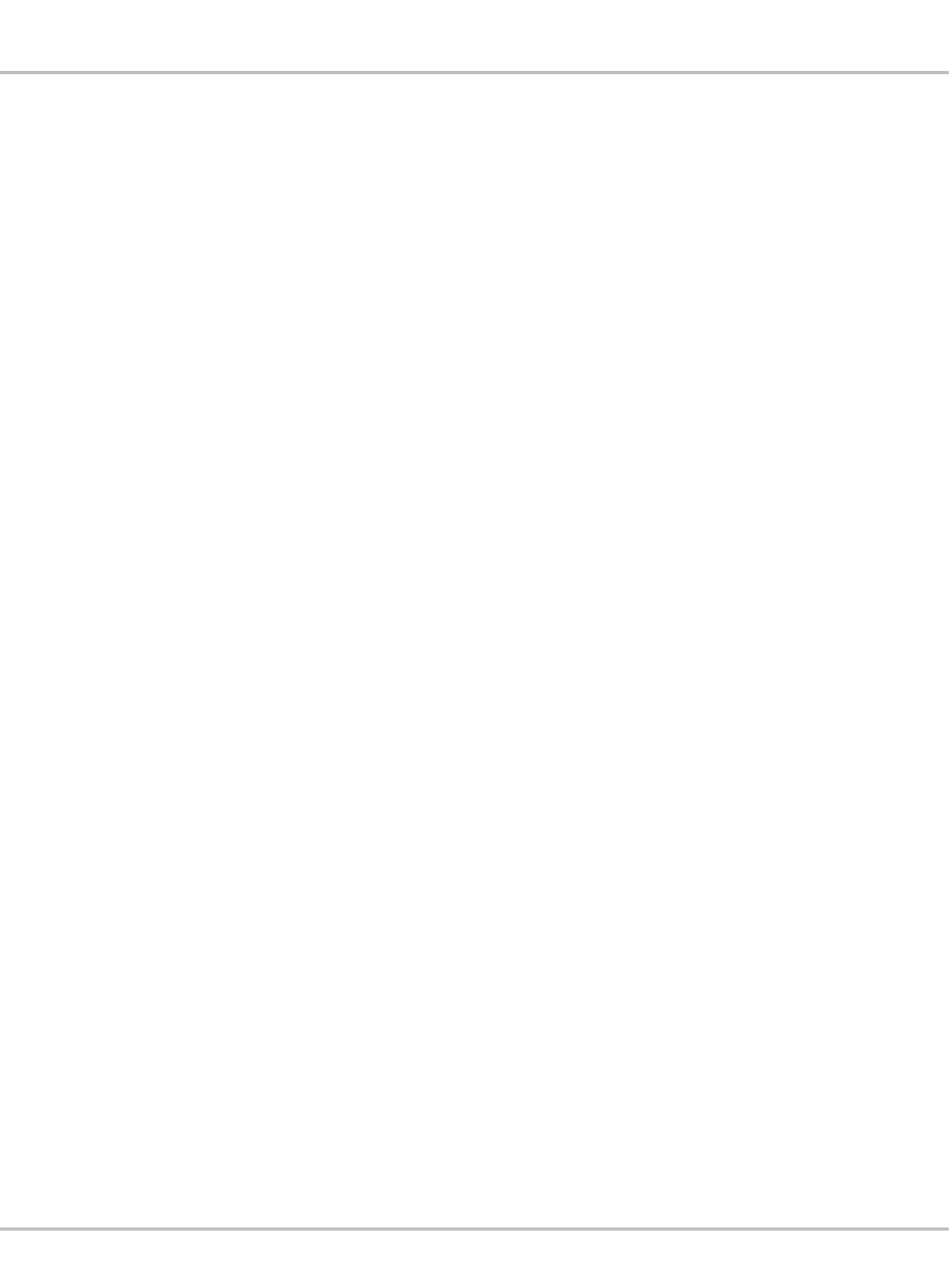
(2) Check and make sure the pulley rotation follows the same direction as labels.
(3) Make sure all the stand casters are locked or fixed in position.
(4) Keep the working area clean from obstacles.
5. During Operation
(1) Always keep your fingers, hair, or clothing away from the moving components and moving area. Do not place
your personal belongings on the machine.
(2) The machine is designed to run at high speed. Always keep your hands away from the moving area. Do not
resume the work cycle until the machine stops completely.
(3) Be careful not to be caught by the machine or components when removing or resetting the machine.
(4) To avoid accident caused by abrupt start, when performing service on the motor or belt, make sure the power is
off and the machine stops completely.
(5) A servo motor is silent as the machine stops. Be sure to turn off the power to avoid an abrupt start.
(6) Always keep the fan and airway of the power cabinet clean from any obstacle.
6. Lubrication
(1) Apply only qualified oil and grease onto the parts as instructed in the manual.
(2) If the lubricant contacts your eye or body, wash it off immediately. Consult a medical care if necessary.
(3) If the lubricant goes into your body accidentally, go to the nearby medical care immediately.
7. Service
(1) Only a certified engineer/technician is allowed to perform service to the machine, including adjusting and
repairing. Use only genuine parts for replacement. Our company assumes no responsibility/liability for any
accident caused by improper repair or adjustment, or the use of any parts other than genuine one.
(2) Only a certified technician or authorized engineer is allowed to repair or maintenance the electric system.
(3) When performing service to air-driven parts, like an air cylinder, first disconnect the air supply and expel the air
completely to avoid abrupt start.
(4) Check all screws and nut are fixed well after adjusting and replacement.
(5) A periodical cleaning is necessary. Make sure the power is off and the machine stops completely before cleaning.
(6) If the machine functions poorly or abnormally, stop the operation and turn off the power. Contact the authorized
dealers or us to request for a technical service support.
(7) When there is a fuse failure, turn off the power, find out the cause of the failure and apply solution to it, then
replace with a new one with the same spec.
(8) Periodically check and clean the fan airway and the cable/wiring.
8. Working Environment
(1) The machine should be free from the affection of electro-magnetic wave.
(2) The power supply should be in good and reliable condition, the fluctuation of rated voltage should be less than
10%.
(3) Always check the air pressure and quality. Some extra device might be needed if the supply is not reliable.
(4) The machine is designed to be used with ambient temperature 5°C ~ 35°C, relative humidity 35%~85%.
(5) To protect the electronic components and for safety cause, when there is a frost resulting from a dramatic
temperature rise, disconnect the power and wait until it dry completely.
(6) For safety cause, when there is a thundering or lightening, stop the operation and disconnect the power supply.
(7) Do not use TV or radio nearby the machine as to avoid interference.
(8) Apply necessary protection during operation. Follow applicable regulations set by local administration.
(9) For disposal of packages, lubricant, and product, please follow the applicable regulations set by local
administration.