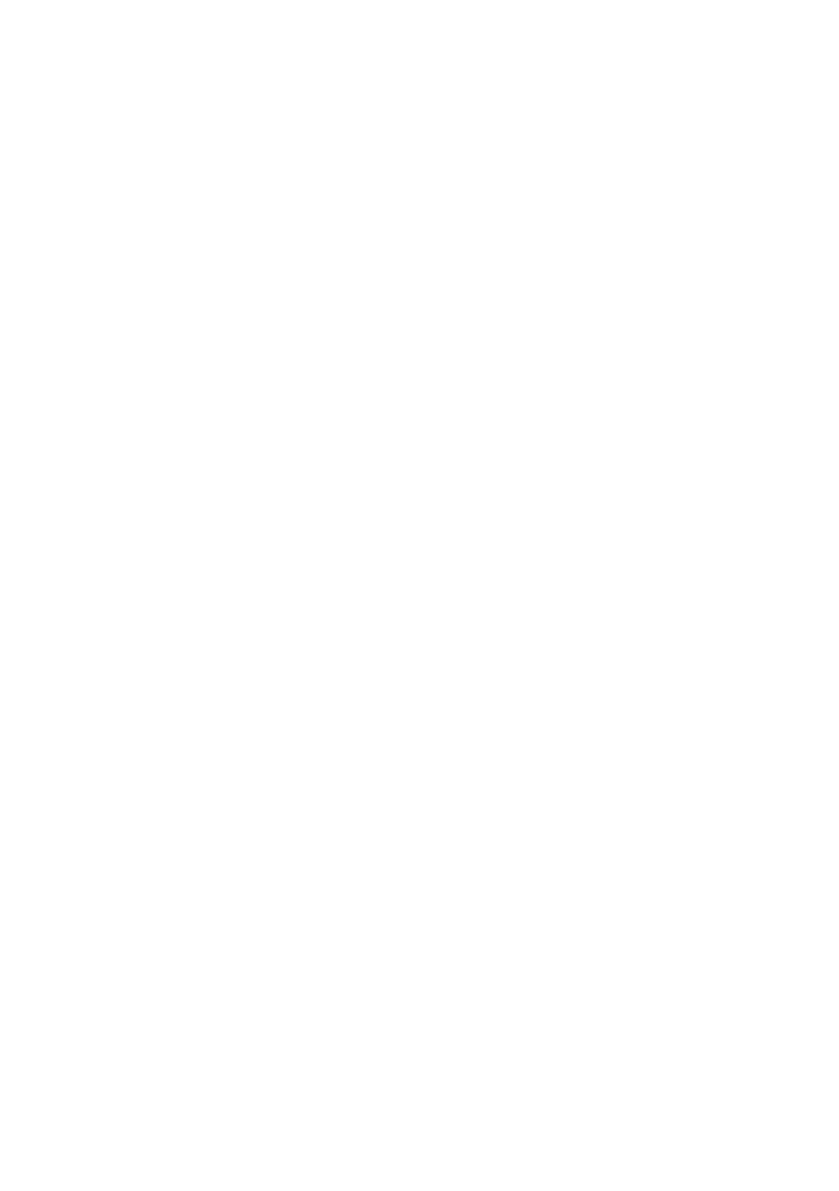
12 03528635_ed7
16. Position the Bearing nearest the smaller spline on the shaft of
the First Stage Intermediate Gear above the bearing recess in the
Gear Box Frame. Engage the smaller spline of the Gear with the
spline of the Second Stage Intermediate Gear while pushing the
Bearing into the recess.
17. Using a piece of tubing that contacts the inner ring of the
Intermediate Gear Pinion Rear Bearing (24), press a Bearing onto
the shaft of the Intermediate Gear Pinion.
18. Place the remaining Gear Box Gasket onto the Gear Box Frame
making certain the Gasket ts over the alignment pin in the
Frame and ts well around the large, raised alignment hub.
19. Position the Gear Box (18) over the assembly and bring the Gear
Box down against the Gasket while making sure the Bearings
enter the bearing recesses in the Gear Box. Make certain the
alignment pin and hub on the Frame enter the hole and recess
in the Gear Box.
20. While keeping the assembly together, turn it over and insert the
eleven Gear Box Cover Cap Screws (41) with their Lock
Washers (42) through the holes of the Cover and Frame and into
the Gear Box. Tighten the Screws evenly, a little at a time, using
an alternating pattern. Use the Screws to draw the assembly
together without distortion and without binding.
Assembly of Series 92NA and 92RA Gearing
1. Insert the two Motor Shaft Gear Keys (26) into the slots in the
Motor Shaft (36) and press the Motor Shaft Gear (34) onto the
Motor Shaft.
2. Using a dowel, push the Motor Shaft Seal (39), small opening
leading, into the recess in the Gear Box Cover Assembly (38).
3. Using a piece of tubing that contacts the inner ring of the Motor
Shaft Front Bearing (35), press the Bearing onto the output end of
the Motor Shaft.
4. Using a piece of tubing that contacts the inner ring of the Motor
Shaft Rear Bearing (24), press a Bearing onto the motor end of the
Motor Shaft.
5. Insert the output end of the Motor Shaft through the Motor Shaft
Seal and push it into the into the gear Box Cover Assembly until
the Motor Shaft Front Bearing seats in the bearing recess.
6. Using a piece of tubing that contacts the inner ring of the First
Stage Intermediate Gear Front Bearing (23), press the Bearing
onto the shaft adjacent to the small spline of the First Stage
Intermediate Gear (21).
7. Using a piece of tubing that contacts the inner ring of the First
Stage Intermediate Gear Rear Bearing (22), press the Bearing
onto the shaft adjacent to the large spline of the First Stage
Intermediate Gear (21).
8. Place the Gear Box Cover Assembly on a workbench with the
output end of the Motor Shaft downward.
9. Position the Bearing nearest the smaller spline on the shaft of
the First Stage Intermediate Gear above the bearing recess in the
Gear Box Cover. Engage the smaller spline of the Gear with the
spline of the Motor Shaft Gear while pushing the Bearing into the
recess.
10. Place the Gear Box Gasket (20) onto the Gear Box Cover making
certain the Gasket ts over the alignment pin in the Cover and ts
well around the large, raised alignment hub.
11. Position the Gear Box (18) over the assembly and bring the Gear
Box down against the Gasket while making sure the Bearings
enter the bearing recesses in the Gear Box. Make certain the
alignment pin and hub on the Frame enter the hole and recess
in the Gear Box.
12. While keeping the assembly together, turn it over and insert the
eleven Gear Box Cover Cap Screws (41) with their Lock
Washers (42) through the holes of the Cover into the Gear Box.
Tighten the Screws evenly, a little at a time, using an alternating
pattern. Use the Screws to draw the assembly together without
distortion and without binding.
Motor Assembly
1. The Gear Case Gasket (17) has adhesive on one side of the Gasket.
Place one End Plate (7) at on a clean surface with the face having
the channel going from the central opening to the outer edge
upward. Orient the Gasket to the End Plate, making certain the
cylinder dowel hole openings align, and attach it to the End Plate
by bringing the gasket adhesive into contact with the face of the
End Plate. Press it at onto the face.
2. Slip the End Plate, gasket face trailing, onto the spline end of the
Rotor (12).
3. Install the Front Rotor Bearing Spacer Assembly (14) and the
Front Rotor Bearing (13) onto the splined shaft of the Rotor and
against the End Plate. If the Bearing is a tight t on the shaft, use
a piece of tubing that contacts the inner ring of the Bearing and
clears the rotor shaft to press the Bearing onto the shaft.
4. While holding the Rotor in a vertical position, grasp the spline in
copper-covered vise jaws.
5. Place a Vane (10) in each vane slot.
6. Install new Cylinder Seals (8A) in the grooves in the large hubs of
the Cylinder (8).
7. For Series 92N Non-reversible Motors, the direction of rotation of
the Motor depends on the relationship of the Cylinder and End
Plates. To obtain desired shaft rotation, proceed as follows:
a. Rotate the End Plate until the 17/64” (6.75 mm) through hole
(dowel hole) is facing you. Note there is a similar hole extending
lengthwise through the Cylinder, and at about 40 to one side of
the hole is an air port.
b. Hold the Cylinder upright, facing the dowel hole and with
the air port to the right for clockwise shaft rotation, to the left
for counterclockwise shaft rotation. Then place it over the Rotor
so that the dowel hole in the Cylinder and End Plate are in
alignment. For Series 92R Reversible Motors, place the Cylinder
over the Rotor so that the dowel hole in the Cylinder and End
Plate are in alignment.
8. The Gear Case Gasket has adhesive on one side of the Gasket.
Place the remaining End Plate at on a clean surface with the face
having the channel going from the central opening to the outer
edge upward. Orient the Gasket to the End Plate, making certain
the cylinder dowel hole openings align, and attach it to the End
Plate by bringing the gasket adhesive into contact with the face
of the End Plate. Press it at onto the face.
9. Install the End Plate, Gasket side trailing, onto the short hub of
the Rotor. Rotate it so that the cylinder dowel hole is aligned with
the corresponding hole in the Cylinder. Insert the Cylinder Dowel
(9) to maintain the alignment with the Dowel protruding through
the Rear End Plate.
10. Slide the Rear Rotor Bearing (5) on the short hub of the Rotor and
against the End Plate. Using snap ring pliers, install the Rear Rotor
Bearing Retainer (6) to keep the Bearing and End Plate in position.
11. Position the Motor Housing Cover (1) over the Rear Rotor Bearing
and End Plate. Make certain the cylinder dowel holes and porting
are aligned correctly. Remove the assembly from the vise jaws.
12. Carefully slide the Motor Housing (11) over the assembled motor
and position it against the Motor Housing Cover.
13. Position the assembled Gear Box (18) against the face of the
Motor Housing. Make certain the spline of the Rotor engages the
teeth of the First Stage Intermediate Gear (21) properly.
14. Install the Housing Cover Cap Screws (2) along with the
Washers (4). With the motor running at a slow speed
(30 to 40 psig) (267 to 276 kPa) alternately tighten the
Screws to 28 to 31ft-lb. (38.0 to 42.0 Nm) torque.