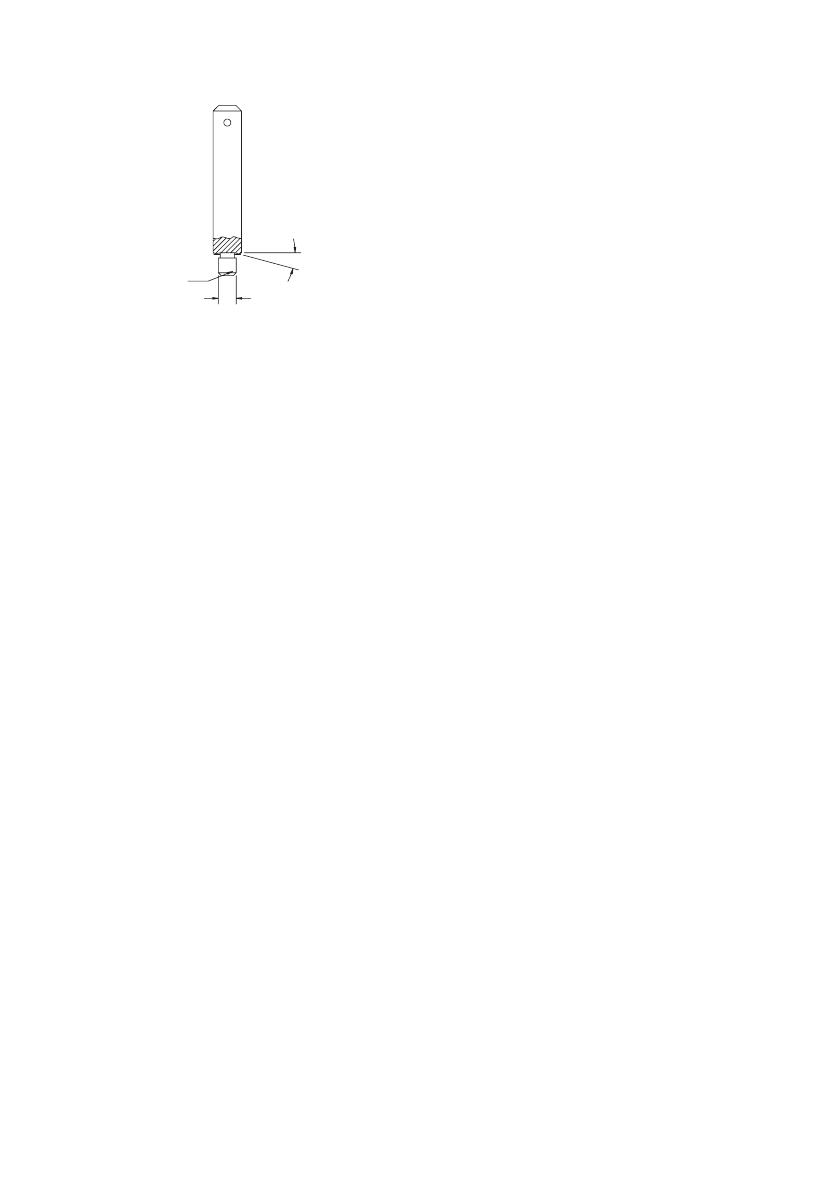
03523545_ed15 11
Shoulder to
regulate depth
Pilot to t I.D. of bearing
length of pilot to be
approximately 1/8” less
than length of bearing
15˚
Needle Bearing inserting tool
(Dwg. TPD786)
Assembly of the Gearing
1. For P, Q, S or U ratio, if the Spindle Planet Gear Bearings (49) were
removed from the Spindle Planet Gears (48), press new Bearings into
the Gears using a needle bearing inserting tool. Press one Bearing
in from each end of the Gear until they are ush with the face of the
Gear. If any Gears are damaged, install a complete new set of Gears.
Do not mix old Gears with new Gears in the same motor.
For K, M or N ratio, if the Spindle Planet Gear Bearings (35 or 43)
were removed from the Spindle Planet gears (34 or 42), press new
Bearings into the Gears using a needle bearing inserting tool. If
any Gears are damaged, install a complete new set of Gears. Do
not mix old Gears with new Gears in the same motor.
2. For D ratio, support the web at the output end of the
Spindle (37) on the table of an arbor press and position the Spindle
Drive Plate (41) inside the web making certain that the pin holes are
in alignment. The holes in the webs of the Spindle are tapered and
smaller toward the output end of the Spindle. Press both Spindle
Drive Plate Shafts (40) through the rear web and Drive Plate into the
front web until the Shafts are ush with the face of the rear web.
For all other ratios, support the web at the output end of the
Spindle (31, 37 or 45) on the table of an arbor press and position
a Spindle Planet Gear with Bearings in the web. The holes in the
webs of the Spindle are tapered and smaller toward the output
end of the Spindle. Press a Spindle Planet Gear Shaft (33, 39 or 47)
through the rear web and Bearings into the front web until the
Shaft is ush with the face of the rear web.
3. For all ratios except D ratio, repeat Step 2 with the remaining
Spindle Planet Gears and Bearings.
4. Stand the Spindle, output end upward, on the table of an arbor
press and using a piece of tubing that will clear the Spindle, press
the Spindle Front Bearing (32, 38 or 46) onto the Spindle.
5. Invert the Spindle and without applying pressure to the Spindle
Front Bearing, press the Spindle Rear Bearing (36, 44 or 50) onto
the short hub of the Spindle.
6. For P, Q, S or U ratio, align one of the exterior slots on the Internal
Gear (57) with the two Internal Gear Keys (58) located opposite
the Grease Fitting (60) in the Gear Case (59). Push the Internal Gear
into the Gear Case until it stops against the gear teeth in the Case.
7. Apply lubricant to the gearing and shaft and insert the assembled
Spindle, output end leading, into the end of the Gear Case with
the largest opening. Push the assembly into the Gear Case until
the Spindle Front Bearing seats in the gear case bearing recess.
8. For P, Q, S or U ratio, if the Gear Head Planet Gear Bearings (53)
were removed from the Gear Head Planet Gears (52), press new
Bearings into the Gears using a needle bearing inserting tool. If
any Gears are damaged, install a complete new set of Gears. Do
not mix old Gears with new Gears in the same motor.
9. For P, Q, S or U ratio, support the web at the spline shaft end of
the Gear Head (51) on the table of an arbor press and position a
Gear Head Planet Gear with a Bearing in the web. The holes in the
webs of the Gear Head are tapered and smaller toward the spline
shaft end of the Gear Head. Press a Gear Head Planet Gear
Shaft (54) through the rear web and Bearing into the front web
until the Shaft is ush with the face of the rear web.
10. For P ratio, insert the Rotor Pinion (55) into the center of the Gear
Head. This must be done before installing the second Gear in the Gear
Head. It cannot be installed after a second Gear is secured in position.
11. For P, Q, S or U ratio, repeat Step 9 with the remaining Gear Head
Planet Gear and Bearing.
12. For P, Q, S or U ratio, stand and support the assembled Gear
Head on the table of an arbor press with the spline shaft end
downward and press the Gear Head Bearing (56) onto the hub of
the Gear Head.
13. For P, Q, S or U ratio, apply lubricant to the gear head gearing
and while engaging the spline of the Gear Head with the gearing
of the Spindle and Internal Gear, slide the assembled Gear Head
into the Gear Case.
Assembly of the Motor
1. Push the Rear End Plate (15), at face leading, onto the short hub
of the Rotor (17).
2. Push the Rear Rotor Bearing (14) onto the short hub of the Rotor
into the recess of the Rear End Plate and install the Rear Rotor
Bearing Retainer (13) in the groove on the shaft of the Rotor to
retain the Bearing and End Plate.
3. Place a Vane (18) in each vane slot in the Rotor and place the
Cylinder (19) down over the Rotor and Vanes and against the Rear
End Plate. Make certain the holes in the Cylinder and End Plate
can be aligned. If they don’t align, invert the Cylinder.
4. Press the Front Rotor Bearing (21) into the bearing recess of the
Front End Plate (20).
5. Press the Front Rotor Bearing, Front End Plate leading onto the
spline end of the rotor shaft until the End Plate contacts the
Cylinder.
6. Use a 1/8” rod approximately 12” long to align the cylinder dowel
holes in the Front End Plate, Cylinder and Rear End Plate. Insert
the end of the rod at the Rear End Plate end into the dowel hole
in the Motor Housing. Slide the assembled motor along the rod
into the Motor Housing until it stops against the bottom of the
motor bore.
7. Remove the assembly rod and install the Cylinder Dowel (16) in
its place.
8. Install the two Motor Retaining Washer (22), the concave face of
both Washers trailing, over the hub of the Front End Plate.
9. For D, K, M or N ratio, install the Motor Spacer (30) over the rotor
shaft and into the Motor Housing against the Motor Retaining
Washers.
10. Install the assembled Gear Case against the Motor Housing.
It may be necessary to rotate the Spindle by hand to properly
engage the gearing with the spline on the Rotor.
11. Secure the Gear Case to the Motor Housing with the three Gear
Case Cap Screws (11) and Lock Washers (12).
12. For Models with Piped-Away Exhaust, install new Exhaust
Deector Seals (6 and 7) in the internal grooves at each end of
the Exhaust Deector (5).
13. Slide the Muer (8) over the rear of the Motor Housing until it
stops against the body of the Housing.
14. Slide the Exhaust Deector over the rear of the Motor Housing
and Muer until it stops against the forward Exhaust Deector
Retaining Ring (9).
15. Position the Backhead Gasket (3) against the rear face of the
Motor Housing.
For Series 4800 Non-reversible Motors, position the Gasket to
block o the holes in the quadrant marked with an “R” if forward
rotation is desired, or to block o the holes in the quadrant with
an “F” if reverse rotation is desired.
For Series 4840 Reversible Motors, position the Gasket so that
each gasket inlet port aligns with a group of three holes through
the housing rear wall.
16. Place the Backhead against the Gasket. Install the three Backhead
Cap Screws (11) and Lock Washers (12) to secure the Backhead
and Exhaust Deector to the Motor Housing.
17. Install one Air Strainer (1) for non-reversible models and two Air
Strainers for reversible models in the Backhead (2).