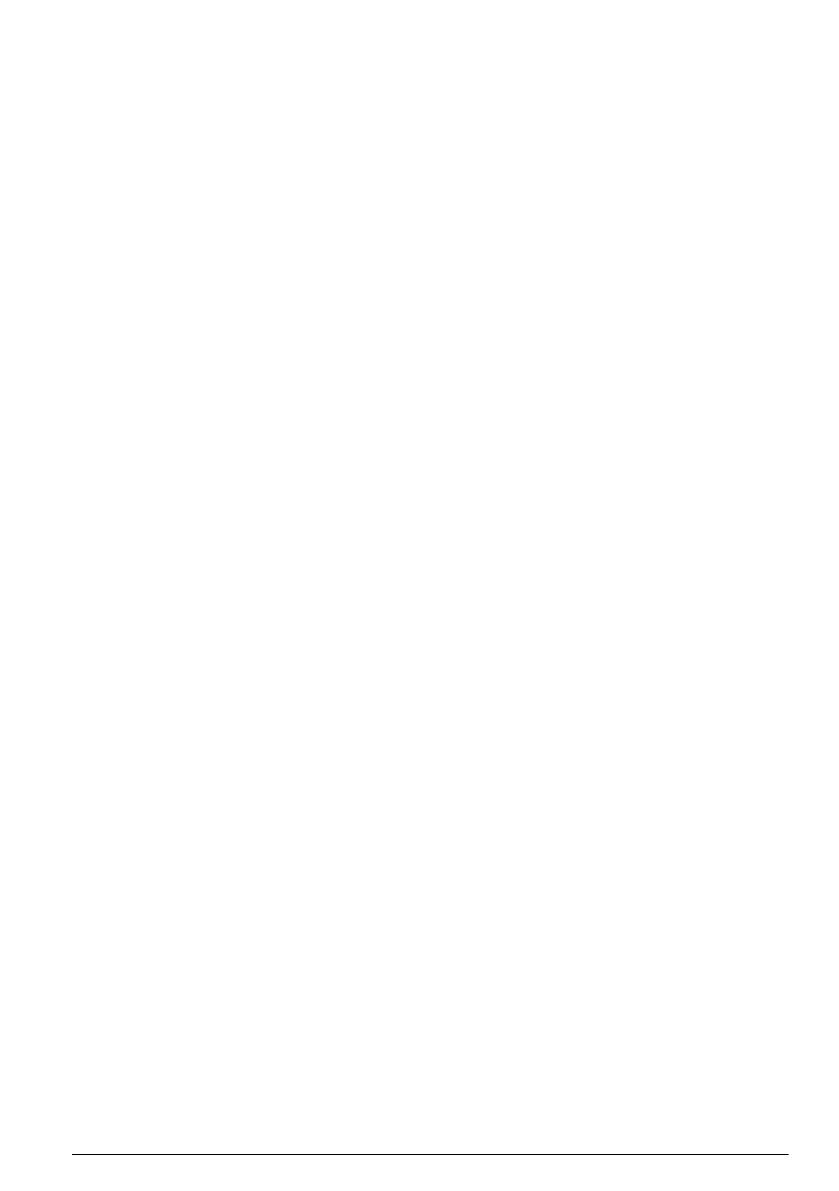
1. Push New calibration. A calibration screen is displayed showing the gas purity data of the main
gas. If the value is incorrect, enter the correct value in the Gas purity box.
2. When the measurement stabilizes press the Validation First Point button. A new measurement
is then initialized and the internal air pump automatically activated.
3. When the measurement stabilizes press the Validation Second Point button.
4. You now have the opportunity to accept the calibration, store the new values, and write the
details to the calibration report file. If the calibration cannot be performed, an error message will
be displayed giving the reason.
Flow sensor
1. Push New calibration. A calibration screen is displayed and the instrument will then compute the
measured flow in four steps (at 0.200 mL/s, 0.400 mL/s, 0.800 mL/s and at 0.000 mL/s). The
results are displayed on screen.
2. After a few minutes, when the process is complete, the Validation button is highlighted. Press
this button to accept the calibration (you will need to confirm acceptance).
Oxygen sensor
The O
2
sensor is calibrated in-situ with an air pump providing a continuous flow of fresh air in front of
the sensor head.
1. Push New calibration. A calibration screen is displayed.
2. The value Ratio ideal membrane is a percentage of the current against the ideal current for the
membrane being used.
3. The value Variation shows the percentage of this measurement against the last sensor
calibration measurement.
4. The Calibration Status box at the bottom of the screen shows the current calibration process
with a bar graph below it to indicate the progress.
5. On completion, only if the calibration is valid will the Validation button be displayed. Press this
button to accept the calibration, store the new values, and write the details to the calibration
report file. If the calibration cannot be performed, an error message will be displayed giving the
reason.
Measurement process
Main screen
The initial screen displays standard information about the package to measure. You have the
possibility to change the user and the package type to be measured.
Start analysis
Note: Once a sample has completed the measurement process it will contain a small amount of antifoam.
Therefore, after measurement, ensure the sample is disposed of in a sink (or similar) to avoid any risk of ingestion.
For optimal operation, the base of the package holder should always have a layer of water for
improved transfer of the ultrasound energy to the liquid in the package. For the correct amount of
water, tilt the package holder forward by turning the tilt knob to position 3 (small can icon). Next, fill
the holder with water until the water level reaches the top without spilling over. Finally, put the holder
back to the correct tilt position for the package to be measured in readiness for the measurement
process.
Select the Start Analysis option to start the measurement process. The instrument will display
information regarding the measurement step being taken, instructions on any user involvement
required, and the measurement progress throughout the duration of the measurement process.
The first screen gives details of the package being analyzed and gives the user information on what
action to take. As instructed, raise the transparent front door in order to place the package in the
English
17