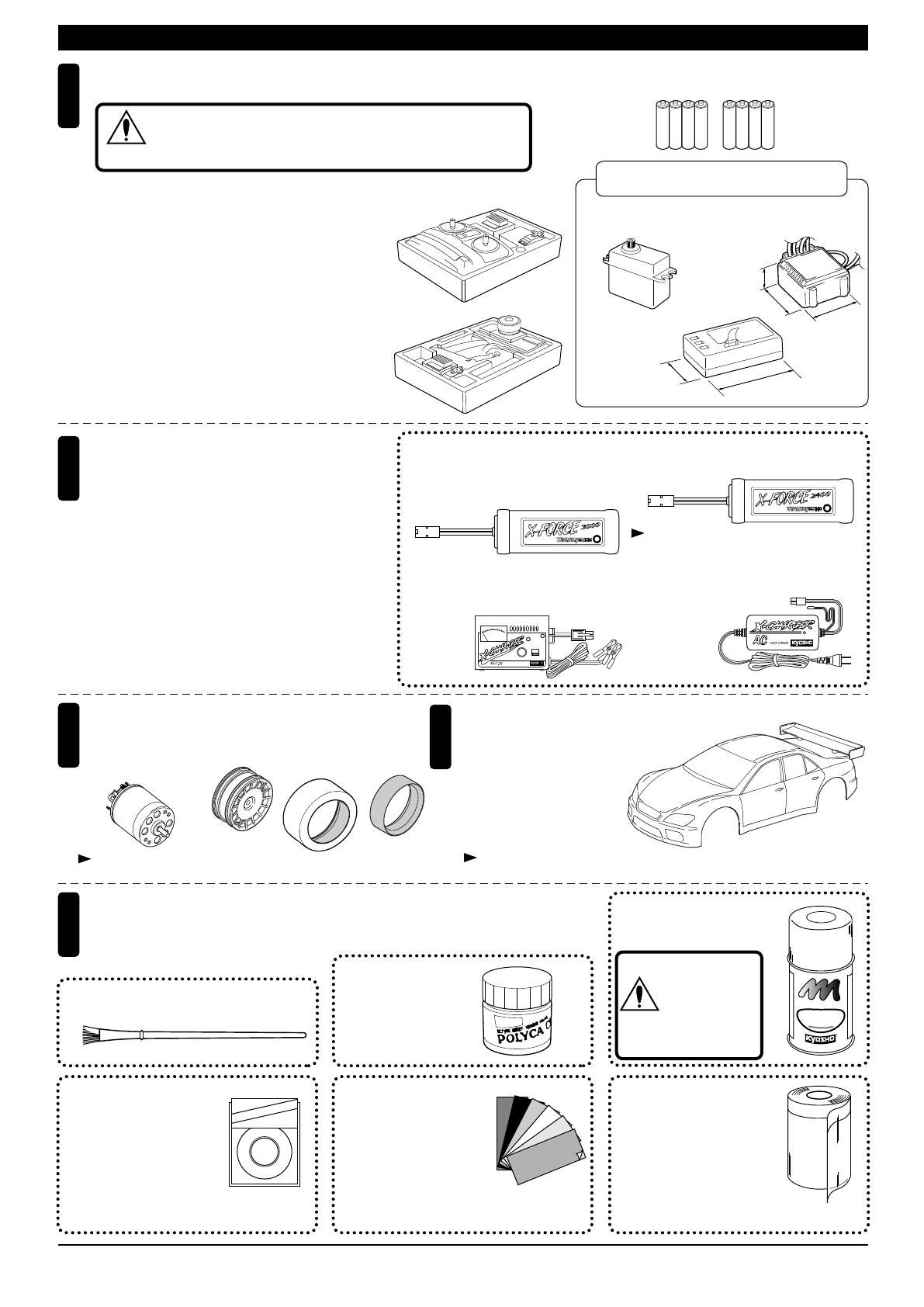
2
Standard Size Servo
Approx. 30mm
Approx. 50mm
Receiver
2
PAINT BRUSH
5
Paint and Brush
REQUIRED FOR OPERATION (1)
M
i
c
ron Line
Ta
p
e
KYOSHO
MICRON LINE TAPE
No.1841
1842
1843
1859
1860
(1mm x 5m)
(1.5mm x 5m)
(2.5mm x 5m)
(0.4mm x 8m)
(0.7mm x 8m)
MASKING SHEET
No.1947
Suitable servos, receiver & electric speed controller
POLYCA COLOR
No.2230
D FLEX COLOR DECAL
No.96701
Operation/Receiver Battery
A single Ni-Cd battery powers operation and recei-
ver. Batteries listed right are suitable.
and Charger for Ni-Cd Battery
Two types of chargers are available. One operates
on a 12V car battery. The other operates on a 100V
house outlet.
For painting the body, use Kyosho paints
for models!
Super-flexible tape for
masking and detail de-
signing jobs.
Self-adhesive super-flexible sheets that
bond to polycarbonate - even when
applied to curved surfaces.
For safe masking jobs, use this plastic mask-
ing sheet featuring one self-adhesive edge.
AA-size Batteries (For Transmitter)
AAAA
AAAA
Electric Speed Controller
31 40mm
36 43mm
20 29mm
1
2ch with electronic speed controller and 1 servo radio control set
Stick-type
2ch radio set
Wheel-type
2ch radio set
This kit requires a 2 channel radio con-
trol set with electronic speed controller.
Because there are stick-type and wheel-
type transmitters, use which ever fits
your convenience best.
For more information on the radio con-
trol set, refer to its instruction manual.
CAUTION: Only use a surface radio with 2 channels and electronic
speed controller! (Any other radio is prohibited!)
KYOSHO SPRAY COLOR
No.76301 76711
S
P
R
A
Y
C
O
L
O
R
R
K
Y
O
S
H
O
CAUTION: Before
using spray colors,
always read their
explanations!
3
Motor
Tire / Wheel / Inner Sponge
(Pure Ten Size)
Use a 540 size motor.
4
Body
This kit does not include a
body shell. Purchase one
for 1:10 scale cars, with
about 190mm in width.
X-CHARGER DC
X-CHARGER AC
7.2V-3000mAh XFORCE Ni-MH Battery
XFORCE 3000
7.2V-2400mAh Ni-Cd Battery
Gear ratio included in the kit suits 23T motor.
Use tires, wheels and Inner Sponge less than 24mm width.
103AT
for
7.2-8.4V
Ni-Cd & Ni-MH
THE FINEST RADIO CONTROL MODELS
R
Separate Type Battery is also available.
No.71024
NI-CD BATTERY
J
R
M
N
i
-
C
d
Ni-MH
J
R
M
NI-CD BATTERY
X- DC
24mm
7.2V-3000mAh
XFORCE
XFORCE 3000
7.2V-2400mAh
X- AC
190mm 1/10
30mm
50mm