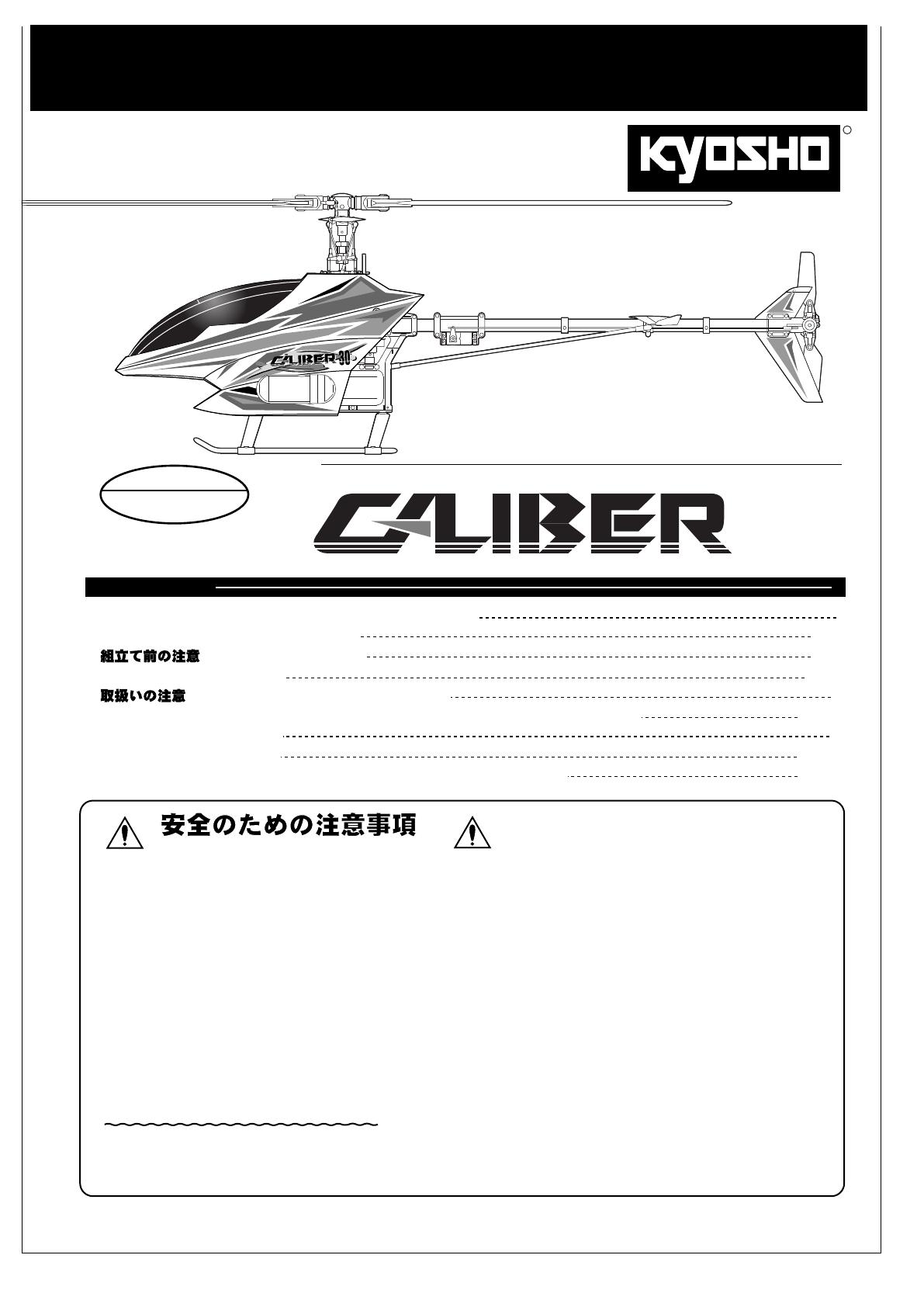
30
THE FINEST RADIO CONTROL MODELS
R
SPECIFICATIONS ARE SUBJECT TO CHANGE WITHOUT NOTICE.
No. 21135/21137
2
3 ~ 4
5 ~ 6
7 ~ 18
19
19 ~ 29
30
31 ~ 35
36 ~ 37
INDEX
INSTRUCTION MANUAL
UNDER SAFETY PRECAUTIONS
This radio control model is not a toy.
This is a kind of machine including a rotor which rotates with
high speed and has a possibility to be dangerous. You are
responsible for this model's assembly, safe operation (place
to fly, frequency) check and adjustment of the model.
Assemble this kit only in places out of children's reach!
Take enough safety precaution before and after operation.
After every flight, inspect screws and nuts for looseness, and
parts for wear. Any damaged parts should be immediately
replaced, repaired or adjusted for safe operation.
Use only Kyosho genuine parts for replacement.
Failing to do so will result in accidents or malfunction of the
model. Kyosho do not take responsibilities for the accidents
and crashes if using the parts which are not Kyosho genuine
ones.
Always keep this instruction manual ready at hand for quick
reference, even after completing the assembly.
RADIO CONTROLLED ENGINE POWERED HELICOPTER
REQUIRED FOR OPERATION
RADIO PREPARATION
BEFORE YOU BEGIN
ASSEMBLY
OPERATING YOUR MODEL SAFELY
SETTINGS ¥ FLIGHT LESSONS ¥ MAINTENANCE
PARTS LIST
EXPLODED VIEW
SPARE & OPTIONAL PARTS
For Advanced Flyers
© 2002 KYOSHO CORPORATION
Before beginning assembly, please read these instructions thoroughly.