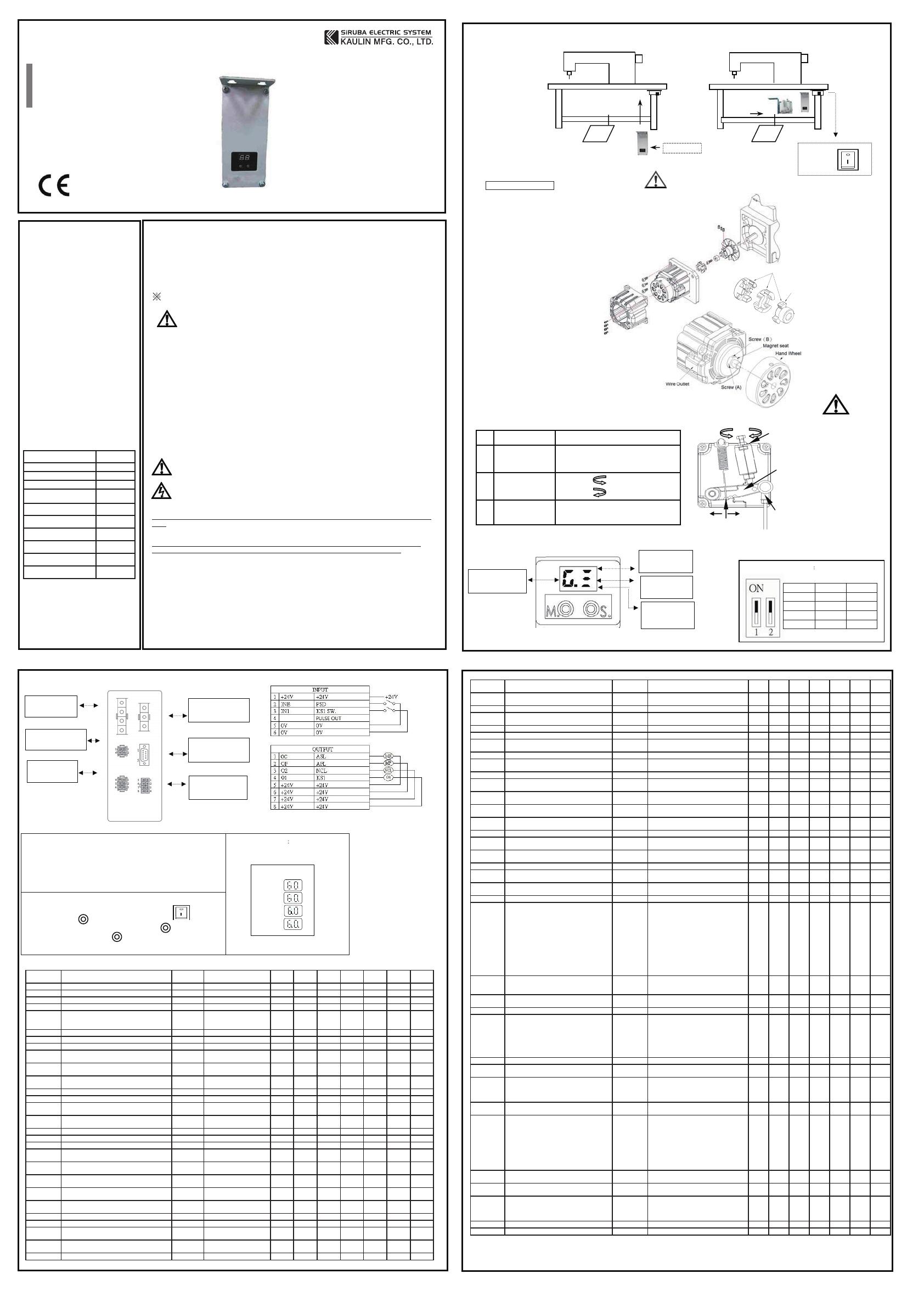
3.1 CONNECTOR DIAGRAM:
4. Adjust step at parameter zone:
Step1: Press “M.” key to enter setting mode.
Step2: Press “M.” key select the parameter you want to adjust.
Step3: Press “S.” key enter the parameter value adjustment.
Step4: Press “M.” key increase the value.
Step5: Press “SET” key to save.
4.1 Motor direction setting:
Press the“ M. ● ”and turn on the power at same
time . Enter the setting mode , press “M. ● ”key to select
C(CW) / CC(CCW). Press“ ● S.”key to save.
4.2 Angle display:
5. General Parameter List :
2. Installation :
GD4 installation
Speed Control Unit adjustment
3. Panel Key Functions :
1. Safety Precaution :
Please read this manual with sewing machine manual thoroughly and pay attention for the
following safety precaution.
˙Installation and operation must be done by the trained personnel, also turn off the power switch and remove the plug
from outlet and wait for 5 minutes before any installation.
˙This product is designed for the specific sewing machines and must not be used for other purposes.
˙Only use the power voltage as described on the name plate of the motor and control box in ±10 % ranges.
※Attention : If the control box is AC 220V system, please don’t connect to the AC 380V
power outlet, otherwise the error will occur and motor is not functional. If that
happened, please turn off the power switch immediately and check the power
voltage. Continue supply the 380V power over 5 minutes might damage the
fuses and burst the electrolytic capacitors and even might endanger the
person safety.
˙In order to prevent abnormal operation, keep the product away from the high frequency machines.
˙Don’t operate in direct sun light、outdoors area and the room temperature is 45°C above or 5°C under.
˙Don’t operate near the heater、dew area and the humidity is 30 % less or 95% more.
˙Don’t operate in dusty、evaporate、combustible gas area, and stay away from corrosive material.
˙Don’t apply heavy objects or excessive force on the power cord, also don’t bend or pull the power cord.
˙In order to prevent the static interference and current leakage, all grounding works must be done properly.
˙After power on the machine for the first time, use low speed to operate and check the correct rotation direction.
˙During machine operation, don’t touch any moving parts.
˙All moving parts must have protective device to avoid the body contact and objects insertion.
˙Maintenance and repair must be done by the properly trained technician, also all the spare parts for repair must be
approved or supplied by the manufacturer.
˙Don’t use any objects or force to hit or ram the product.
Danger and caution signs
Limited Warranty
Warranty period of this product is 1 year from purchasing, or 18 months from our manufacturing
date.
Warranty Detail
Any trouble found within warranty period under normal use condition in conformance with this manual, it will be
repaired free of charge. Repair will be chargeable in the following cases even if within warranty period :
1. Inappropriate use include: wrong connecting high voltage, wrong application, disassemble, repair,
modification by incompetent personnel, or operate the product without the precaution, or operate the
products out of its specification range. Insert odd objects or liquids into the product.
2. Damage by fire, Earth quake, lighting, wind, flood, salt corrosive, moisture, abnormal power voltage and any
other damage cause by the natural disaster or by the inappropriate environments.
3. Dropping after purchase, or damage in transportation by customer himself. (or by customer’s shipping
agency)
Note : We put our best effort and mind in testing and manufacturing for assuring the quality and reliable of this
product. But it is possible this product can still be damaged due to external magnetic interference and
electronic static or noise or unstable power source more than expected; therefore the grounding system of
operate area must be well-connected to this product and it’s also recommended to install a failsafe device.
(such as residual current breaker).
Risks that may cause personal injury or risk to the machine are marked with this
symbol in the instruction manual.
This symbol indicates electrical risks and warnings.
EC Declaration of Conformity
We hereby declare that the following products:
AC servo motor—GD4 series
are in conformity with the provision of the EC
directives as following :
-EC Low Voltage Directive (2014/35/EU)
-EC Electromagnetic Compatibility Directive
(2014/30/EU)
-EC Machinery Directive (2006/42/EC)
Applied harmonized standards :
EN 60204-31 : Electrical equipment of industrial
machines. Particular requirements
for sewing machines, sewing units
and sewing system.
EN 12100 : Safety of machines.
Declaration of Conformity for
Concentration Limits for Certain
Hazardous Substances
We hereby declare that the following products:
AC servo motor—GD4 series
are complies with the following directives and
requirements :
1. European Union RoHS Directive (2011/65/EU) and
the concentration limits for certain hazardous
substances ((EU) 2015/863)
2. People’s Republic of China Electronic Business
Standard : Requirements for concentration limits for
certain hazardous substances in electronic information
products (SJ/T 11363-2006)
Our product itself (motor, control box) or its packing
materials and accessories (box, screws package,
user manual, sticker, label, print…etc.) or the
suppliers of parts and raw materials are all in
conformity with the provision of the European Union
RoHS Directive and People’s Republic of China
Electronic Business Standard to conform the
following concentration limits for the ten hazardous
substances :
Hazardous Substance Permissible
Values
Lead 0001 )bP(
Mercury (Hg) 1000
Cadmium (Cd) 100
Hexavalent chromium (Cr VI) 1000
Polybrominated Biphenyl
(PBB) 1000
Polybrominated Diphenyl ether
(PBDE) 1000
Di(2-ethylhexyl)phthalate
(DEHP) 1000
Butyl Benzyl Phthalate (BBP) 1000
Dibutyl phthalate (DBP) 1000
Diisobutyl phthalate (DIBP) 1000
*The concentration of lead in the lead-free process
for PCB shall be less than 800 ppm.
*For packing materials shipped with our products or
parts, the hazardous substances shall be 80 ppm
or less in sum of Pb+Hg+Cd+Cr VI.
a). Install the motor and control box under the table b). Install the pedal with speed control unit.
GD4 series
Pedal
Components of speed control
unit : see figure
A: Spring for toeing forward
force adjustment
B: Bolt for heeling backward
force adjustment
C: Pedal arm
D: Pitman rod for pedal
Caution :
For person safety, turn off the
power switch and remove the
power plug from outlet before any
adjustment.
1
2
3
Term of adjustment
Toeing forward
force adjustment
Heeling backward
force adjustment
Pedal stroke
adjustment
Adjustment result
Spring A move to right = force increased
Spring A move to left = force decreased
Bolt B turn = force decreased
Bolt B turn = force increased
Rod D secure at right = stroke is longer
Rod D secure at left = stroke is shorter
Motor rotation
direction icon
No position
Needle
Motor Power AC power input
Motor encoder
eed control unit
Output
(Note: Above 3 modes do not display at same time )
Decrease Increase
A
D
C
B
Decrease Increase
Power :
Parameter
NO. 6D 5D 4D 3D 2D 1D 0D eulaV egnaR emaN noitcnuF
BS Front suction function selection ON/OF ON: Valid
OF: Invalid ON ON OF OF OF OF OF
C1 Front suction function stitches setting 0 ~ 99 *1 Stitch 5 20 5 20 5 5 0
ES Rear suction function selection ON/OF ON: Valid
OF: Invalid ON ON OF OF OF OF OF
C2 Rear suction function stitches setting 0 ~ 99 *1 Stitch 35 40 35 40 35 35 99
DS Setting stitches of delay rear suction 0 ~ 20 *1 Stitch 0 0 0 0 0 0 0
BT Front cutter function selection ON/OF ON: Valid
OF: Invalid OF ON OF ON ON ON OF
C3 Setting stitches of front cutter 0 ~ 99 *1 Stitch 5 10 5 16 5 5 5
ET Rear cutter function selection ON/OF ON: Valid
OF: Invalid OF ON OF ON ON ON ON
C4 Setting stitches of rear cutter 0 ~ 99 *1 Stitch 35 40 35 25 35 35 15
WS Air saving function selection ON/OF ON: Valid
OF: Invalid OF OF OF OF OF OF OF
W1 Setting valid stitches of suction for air
saving 0 ~ 99 *1 Stitch 10 10 10 10 10 10 10
W2 Setting invalid stitches of suction for air
saving 0 ~ 99 *10 Stitch 3 3 3 3 3 3 3
C8 Edge sensor function selection ON/OF ON: Valid
OF: Invalid ON ON OF OF ON ON ON
C9 Automatic sewing speed 1 ~ 50 *100spm 20 20 20 25 40 40 20
CA Re-start function at emergency stop ON/OF ON: Valid
OF: Invalid OF OF OF OF OF OF OF
H/L trevni langis cigol NSP BC L:LOW
H:HIGH L L L H L L L
CC Edge sensor signal check 0 ~ 99 *1 Stitch 3 3 3 3 3 3 3
CD Mode selection for foot lifting after
trimming ON/OF ON: Valid
OF: Invalid OF OF OF OF OF OF OF
CE Trimmer function selection ON/OF ON: Valid
OF: Invalid OF OF ON OF OF OF OF
CF Foot lifting active delay timer 2~25 *100ms 2 2 2 2 2 2 2
CG Trimming mode at sensory stop ON/OF/
SU/SD
ON : After the stitches of [C2. ASLC2]
finished, restart section by
automatically.
OF : After the stitches of [C2. ASLC2]
finished, restart section by full hell
back.
SU : After the stitches of [C2. ASLC2]
finished, stops up position , restart
section full-heeling pedal.
SD : After the stitches of [C2. ASLC2]
finished, stops down position ,
restart section by full-heeling pedal.
ON ON ON ON ON ON ON
CH Mode selection for [C2. ASL2] Stitches
sewing A/M
A: One shot sewing.
M: Pedal control and motor can stop at
middle way.
A A A A A A M
CI Tape cutter connection suction on time
setting 0~99 *100 ms 0 0 0 15 15 15 5
CJ Simple suction stitch setting 0~99 *1 Stitch 6 6 6 6 6 6 6
CK Suction output mode setting
AS/NC/
SK/BL/
TK
AS: Suction function output.
NC: Needle clooing output.
SK: Simple suction function output.
BL: Air blower output for tape cutter
function.
TK : tape cutter output. (for duble cutter
function TK2)
AS AS AS BL TK TK TK
CL Foot lifting off delay timer 0~25 *100ms 1 1 1 1 1 1 1
CM Tape cutter connection blower on time
setting 0~99 *10 ms 10 10 10 8 8 8 10
CN Manual tape cutter function ON/OF
ON : Manual tape cutter anytime enable.
OF : Manual tape cutter must detect
sensor
single off .
OF OF OF OF OF OF OF
CP Restart section function select ON/OF ON : Normal stop function.
OF : Auto restart to first section . ON ON ON ON ON ON OF
F1 Safety switch Mode Setting
S6/ST/O
F
/T1/T2
S6 : Machine protection sw.
ST : Cutter protection sw.
OF : No function.
T1 : Cutter output one times. When [ PZ ]
=
D4 valid.
T2 : Cutter output two times. When
[ PZ ]
= D5 valid.
OF OF OF ST T1 T2 OF
F2 Safety switch protection mode NC/NO NC : Normal close
NO : Normal open NO NO NO NO NO NO NO
F3 Knee switch function mode TK/FL TK:Define switch by tape cutter function.
FL:Define switch by footlift function. FL FL FL FL FL FL TK
F4 INB Input function select SF/PT
US/DS
SF:Safety switch function mode
PT:Photoelectric function mode
US:Needle up at emergency stop
DS:Needle down at emergency stop
PT PT PT PT PT PT PT
N/Y daol tluafed yrotcaF LF Factory setting load N N N N N N N
N/Y evas tluafed yrotcaF SF Factory setting save N N N N N N N
NOTE: Selected machine code Enter “PZ” PARAMETER , press S . KEY and hold it to adjust digit 0~9.
Needle up
Angel Value Display Value
60
160
360
260
Input
Caution :
For person safety, turn off the power switch and
remove the power plug from outlet before any
adjustment.
DIP-SWITCH Adjustment:
1 2 PULSE
OFF OFF 48
ON OFF 36
OFF ON 2
ON ON 1
●●
Parameter
NO. Function Name Range Value D0 D1 D2 D3 D4 D5 D6
P0 Maximum sewing speed 10 ~ 70 *100spm 60 50 26 40 45 45 40
52 52 52 52 02 52 52 mps01* 05 ~ 01 deeps woL 1P
P2 Motor's pulley dimension 1 ~ 160 *1m/m 75 75 75 75 75 75 75
P3 Machine's pulley dimension 1 ~ 160 *1m/m 75 75 75 75 75 75 75
P4 Pulley's ratio setting mode selection ON/OF
ON: Refer to P2.P3
OF: Calculate
Automatically
ON ON ON ON ON ON ON
P5 Sewing speed ─ *100spm --- --- --- --- --- --- ---
P6 Virtual up A position edge angle 0 ~ 359 *1o 0 0 0 0 07 0 0
P7 Virtual down A position edge angle 0 ~ 359 *1o .08 .08 .08 .08 0.8 .08 .08
P8 Single positioning signal synchronizer ON/OF ON: Valid
OF: Invalid OF OF OF OF OF OF OF
P9 Define the UP positioning signal mode H/L L/H L:LOW
H:HIGH L L L L L L L
PA Slow start operation mode ON/OF ON: Valid
OF: Invalid OF OF OF OF OF OF OF
04 04 04 04 04 04 04 mps01* 05 ~ 01 deeps trats tfoS BP
PC Stitch numbers for soft start 1 ~ 9 *1 Stitch 2 2 2 2 2 2 2
PD Slow start setting for first stitch sewing
when the power ON ON/OF ON: Valid
OF: Invalid OF OF OF OF OF OF ON
PE Motor braked at normal stop ON/OF ON: Valid
OF: Invalid OF OF OF OF OF OF OF
PF Weak braking torque scale 0.1 ~5.0 Ampere value 2.0 2.0 2.0 2.0 2.0 2.0 2.0
PG Acceleration time adjustment 10 ~ 50 *10ms 20 20 14 20 20 20 20
PH Deceleration time adjustment 10 ~ 50 *10ms 20 20 16 20 20 20 20
PI Reverse angles function selection ON/OF ON: Valid
OF: Invalid OF OF OF OF OF OF OF
PJ Reverse angles through Needle down and
up 0 ~ 30 *10o .08 .08 .08 .08 .08 .08 .08
PK Needle up function for full heeling pedal ON/OF ON: Valid
OF: Invalid OF OF OF OF OF OF OF
PL Inching sewing function ON/OF ON: Valid
OF: Invalid OF OF OF OF OF OF OF
PM Press down the pedal just half stitch after
needle up function ON/OF ON: Valid
OF: Invalid OF OF OF OF OF OF OF
02 02 02 02 52 02 02 mps01* 05 ~ 01 deeps pu eldeeN NP
52 ~ 1 emit no rettuc epaT OP *100ms 1 1 1 1 1 1 1
PP Direct drive type or belt drive type ON/OF ON: Valid
OF: Invalid ON ON OF ON ON ON ON
PQ Cancel foot lifting at half-heeling pedal ON/OF ON: Valid
OF: Invalid OF OF OF OF OF OF OF
6D ~ 0D edoC enihcaM ZP ─ D0 D1 D2 D3 D4 D5 D6
b). Adjust on position
1. Takes off hand wheel of sewing machine.
2. Turns the shaft gets the scale stop at highest point
(or the point of up position in sewing machine).
3. Turn the encoder disc and the screw (A) to aim at
wire outlet of motor.
Remark: above description is a standard of position adjustment,
if the position is not satisfy pleases adjust till it match
your requirement.
5 OOverlock Mode
a). Motor Installation
1. Takes off the heat exhaust fan and pulley of sewing machine.
2. Puts coupling into shaft of sewing machine, heat exhaust fan
closes to shaft. Fix coupling in shaft by bushing.
Caution:in case the sewing machine dose not reserve screw hole
3. Fix the set screw of coupling。
Warning:clamp sets crew of coupling mustfix in flat surface of shaft or
carve.
4. Fix M 5 motor on fan cover.
Warning: there is against dull design for coupling of sewing
and motor, joint direction must pay more attention
on it.there is against dull design for coupling
of sewing and motor, joint direction
must pay more attention on it。
5. Fix fan cover of motor.
There is against dull design for coupling of
sewing and motor , joint direction must pay
more attention on it.
Clamp sets crew of coupling must
fix in flat surface of shaft or carve.
電控參數說明書
ELECTRONIC CONTROL PARAMETER MANUAL
700KS(RSK)
HF008A/CE
VC008/CE