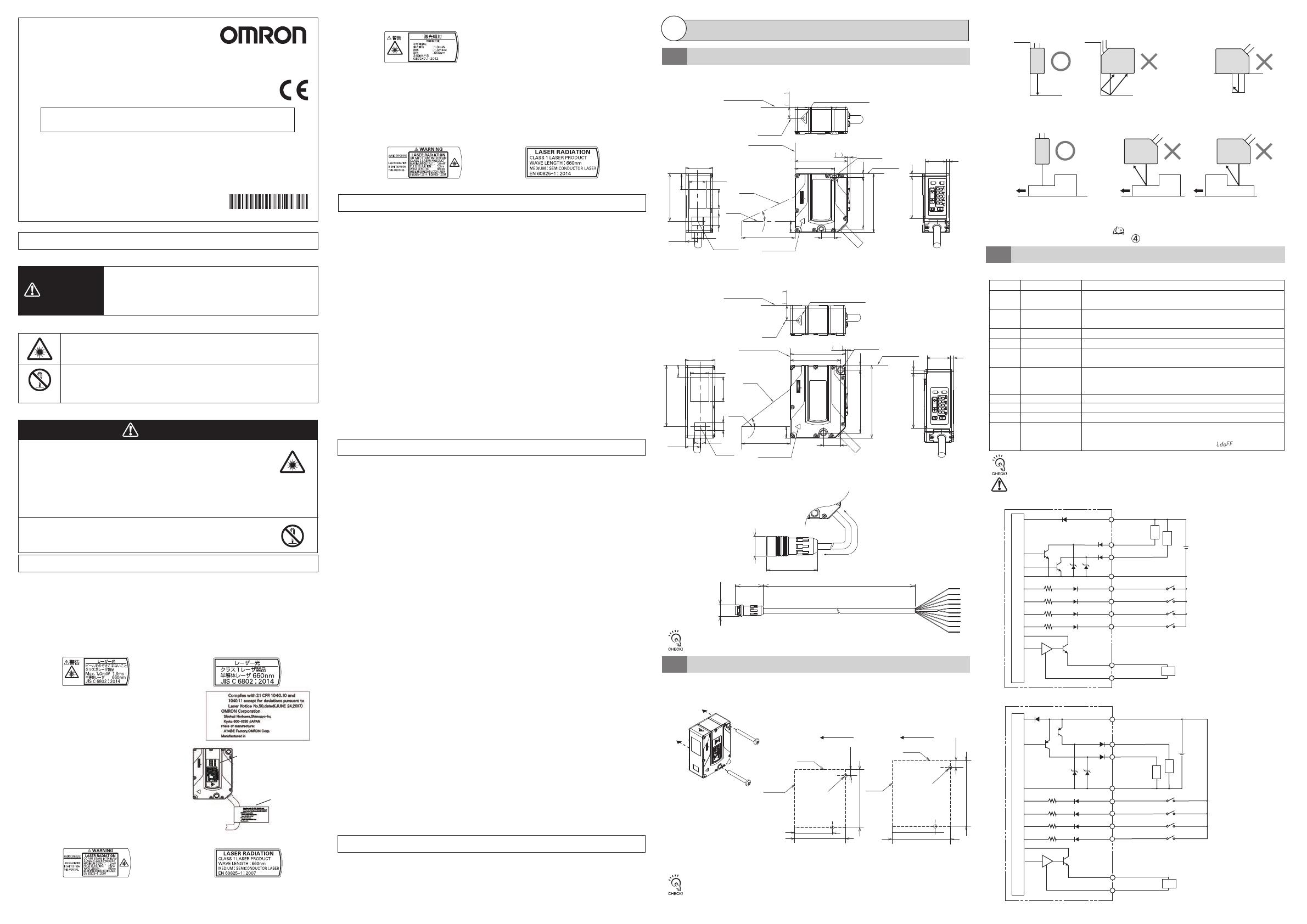
-1- -2-
Laser WARNING label(FDA)
FDA Certification label
(FDA)
©
OMRON Corporation 2011 All Rights Reserved.
● Meanings of Signal Words
● Alert Statements
Laser Displacement Sensor CMOS Type
Smart Sensor
ZX1-LD
PRECAUTIONS ON SAFETY
SAFETY PRECAUTIONS FOR USING LASER EQUIPMENT
PRECAUTIONS FOR CORRECT USE
Checking the Package Content
Do not disassemble the product. Doing so may cause the
laser beam to leak, resulting in the danger of visual
impairment.
Indicates a potentially hazardous situation which, if
not avoided, will result in minor or moderate injury,
or may result in serious injury or death. Additionally
there may be significant property damage.
INSTRUCTION SHEET
■ Power Supply and Wiring
• Do not impose voltage exceeding the rated voltage: 10 to 30 VDC, including 10% ripple (p-p).
• When supplying power to the Sensor, make sure that the polarity of the power is correct, and do
not connect to an AC power supply.
• Do not short-circuit the load for the open collector output. Short-circuiting the load may cause
re or damage on the Sensor.
• Connect the load correctly. Short-circuiting the load may cause re or damage on the Sensor.
• Keep the load within the rated range. Overloading may result in re or damage on the Sensor.
• Wire the product cable separately from high-voltage or power lines. Placing them in the same
wiring or the same duct may cause induction, resulting in the product malfunction or damage.
• Always turn off the power of the Sensor before connecting or disconnecting the cable or
connector.
• Do not use the Sensor for the safety circuits in nuclear power or life-critical applications.
• Implement safety measures e.g. fail-safe circuits.
■ Installation
• Make sure that all installation screws must be tighten securely.
Tightening torque: M3, 0.5N·m (ZX1-LD50/ZX1-LD100)
M4, 1.2N·m (ZX1-LD300/ZX1-LD600)
■ Others
• Do not attempt to disassemble, deform by pressure, incinerate, repair, or modify this product.
• When disposing of the product, treat as industrial waste.
• If you notice an abnormal condition such as a strange odor, extreme heating of the unit, or
smoke, immediately stop using the product, turn off the power, and consult your dealer.
Laser safety measures for laser devices are stipulated both in Japan and overseas. Here, four
cases are described.
(1) Usage in Japan
The JIS C6802:2014 standard stipulates the safety precautions that users must take according
to the class of the laser product.
The ZX1-LD is classied into class 2 dened by this standard.
The ZX1-LDL is classied into class 1 dened by this standard.
■ Installation Location
Do not install the product in locations subjected to the following conditions:
• Surrounding air temperature outside the rating
• Rapid temperature uctuations (causing condensation)
• Relative humidity outside the range of 35 to 85%
• Presence of corrosive or ammable gases
• Presence of dust, salt, or iron particles
• Direct vibration or shock
• Reection of intense light (such as other laser beams, electric arc-welding machines, or
ultra-violet light)
• Direct sunlight or near heaters
• Water, oil, or chemical fumes or spray, or mist atmospheres
• Strong magnetic or electric eld
• In the water, rain, or outdoors
■ Power Supply and Wiring
• Do not supply the power to the Sensor before checking the I/O wiring.
• Ground the FG terminal when using a commercially-available switching regulator.
• If the power supply line is subject to surges, connect a surge absorber that meets the conditions
of the operating environment.
• Do not turn ON the power after wiring before making sure that the power supply is connected
correctly; there are no faulty connections, e.g. load short-circuits; the load current is correct.
Incorrect wiring may result in failure.
• Use a ZX0-XCR Extension Cable (sold separately) to extend the Sensor’s cable. Use only one
cable. Do not extend the cable for the Sensor to a length exceeding 20 m.
• The display and indicators turn ON after approx. 2.5 seconds after the power is turned ON.
• The sensor is certicated by the UL standard on the assumption of the following installation
conditions.
It is based on the assumption of usage in "Class 2 circuit". Please use it with "Class 2 power supply"
in the United States or Canada. The current rating of overcorrect protection is 0.8A max.
It is certicated as open type. The sensor shall be installed within an enclosure.
Rating of the cable is 30V. Please use it as internal cable wiring only in the end products equipment.
■ Warming Up
• After turning ON the power, allow the Sensor to warm up for approx. 30 minutes prior to use.
The circuitry is not stable immediately after turning the power ON, and the values gradually
change until the Sensor is completely warmed up. When using LD-OFF input for a long period
of time, perform warmng up for more than 30 minutes after cancelling LD-OFF.
■ Maintenance and Inspection
• Always turn OFF the power of the Sensor before connecting or disconnecting the cable or for
making adjustment.
• Do not use thinner, alcohol, benzene, acetone, or kerosene to clean the Sensor.
• If considerable foreign matter or dust collects on the glass surface of the front of Sensor, use a
blower brush (for camera lenses) to blow off the foreign matter. Avoid blowing it off with your
breath. For a small amount of foreign matter or dust, gently wipe with a soft cloth. Do not wipe
hard. The damaged glass surface may result in detection errors.
■ Sensing Object
The product cannot accurately measure the following types of objects: Transparent objects,
objects with an extremely low reective sensor ratio, objects smaller than the spot diameter,
objects with a large curvature, excessively inclined objects, etc.
• Sensor: 1
• Instruction sheet (this sheet): 1 each (Japanese and English)
• FDA Certication label : 1
• Laser Warning Label : 1 each Japanese, English(FDA), English and Chinese)
(The explanatory labels are attached to ZX1-LDL instead of the warning explanation labels.
Japanese, English(FDA) and English))
WARNING
● Explanation of Signs
● Laser beam
Indicates caution on potential laser beam hazard.
● Do not disassemble
Indicates prohibition when there is a risk of minor injury from
electrical shock or other source if the product is disassembled.
WARNING
■ I/O Circuit Diagram <NPN Output Type>
■ I/O Circuit Diagram <PNP Output Type>
Installation
1
Dimensions
1-1
Wiring
1-3
The table below shows individual external I/O wires and their roles.
The individual wire colors and roles are the same between pre-wired and
connector joint models.
Wire the Sensor correctly. Unused wires must be insulated. Incorrect wiring may
result in damage to the Sensor.
Role
Brown
Wire color
Name
Connect to 10 to 30 VDC (including 10% ripple (p-p)). Used as the
common I/Os terminal for all I/O except monitor output for a PNP output type.
0-V power supply terminal. Used as the common I/Os terminal
for all I/O except monitor output for an NPN output type.
Blue GND
Outputs the CH1 judgment result.
White
OUT1 Judgment output
Outputs the CH2 judgment result.
Green
OUT2 Judgment output
TUNE1 input
TUNE2 input
Outputs the current value according to the measurement result.
(4 to 20 mA)
Black
Analog output
0-V ground line for analog output.
Connect this line separately from the blue (0 V) GND.
[Important] When analog output is not used, be sure to connect to blue (0 V).
Shield
Analog GND
Inputs tuning to CH1.
Inputs tuning to CH2.
Pink
Zero reset input
Used to execute or cancel zero reset.
Purple
Red
LD-OFF input
Power supply
Orange
■
■
10.2
A*
L*
1. 9
57
15.5
4.5
45.6
55.8
13.6
10.7
227
10.1
17
13.6
A*
L*
10.2
3.246.1
11. 7
2
35.3
Reference surface
2-3.2 dia.
(Mounting hole)
Receiver
axis
Emitter
axis
10.5
Emitter axis
42.3
10.5
14.23
16.77
10.1
15.1
* ZX1-LD50: L=50, A=21°
ZX1-LD100: L=100, A=11.5°
* ZX1-LD300: L=300, A=6.6°
ZX1-LD600: L=600, A=3.4°
Emitter center
Reference surface
Reference surface
Emitter
axis
Reference surface
2-4.5 dia.
(Mounting hole)
Reference surface
Emitter center
Receiver
axis
Emitter
axis
Thank you for selecting an OMRON product. This sheet primarily
describes precautions required in installing and operating the product.
• A specialist who has the knowledge of electricity must treat the product.
• Please read this manual carefully, and use it correctly after thoroughly
understanding the product.
• Please keep this manual properly for future reference whenever
it is necessary.
■ Labeling on Laser Use
The ZX1-LD has the following WARNING label or explanatory label on the side of the sensors.
Emitter center position mark
Emitter center
position mark
Emitter center position mark
Emitter center
position mark
Vinyl insulated round-shaped robot cable
Dia 6.5 9-wire (cross section of conductor:
0.125 mm2/insulator diameter: 0.7 mm)
Standard length: 2 m
Root section bending disabled length: 0 mm
Minimum bending radius: 39 mm
Vinyl insulated round-shaped robot cable
Dia 6.5 9-wire (cross section of conductor:
0.125 mm2/insulator diameter: 0.7 mm)
Standard length: 2 m
Root section bending disabled length: 0 mm
Minimum bending radius: 39 mm
Reference surface
10 to 30 VDC
Shield: Analog GND
Black: Analog output
300 Ω max.
Current output
4 to 20 mA
Red: LD-OFF input
Purple: Zero reset input
Pink: TUNE2 input
Orange: TUNE1 input
Blue: GND (0 V)
Green: OUT2
judgment output
White: OUT1
judgment output
Brown: 10 to 30 VDC
Load
Load
Internal circuit
Load
Shield: Analog GND
Black: Analog output
Red: LD-OFF input
Purple: Zero reset input
Pink: TUNE2
Orange: TUNE1
Blue: GND (0 V)
Brown: 10 to 30 VDC
Load
Internal circuit
Load
Load
10 to
30 VDC
Current output
4 to 20 mA
300 Ω max.
Green: OUT2
judgment output
White: OUT1
judgment output
PRECAUTIONS FOR SAFE USE
ZX1-LD3006/ZX1-LD6006
■ ZX1-LD506/ZX1-LD1006
15 dia.
37.3 L*
Ø 15.5
39.8
* The length of L is as follows:
ZX0-XC10R: 10 m, ZX0-XC20R: 20 m
The extension cable is the robot cable, the same as the cable of the Sensor Unit.
Vinyl insulated round-shaped robot cable
Dia 6.5 9-wire (cross section of conductor:
0.125 mm2/insulator diameter: 0.7 mm)
Standard length: 0.5 m
Sensor root section bending disabled length: 0 mm
Connector section bending disabled length: 40 mm
Minimum bending radius: 39 mm
To mount ZX1-LD50 and ZX1-LD100, use M3 screws (tightening torque: 0.5 N·m) and
ZX1-LD300 and ZX1-LD600, M4 screws (tightening torque: 1.2 N·m).
Mounting Sensor
1-2
Do not touch the sensor emitter and receiver sections. Correct detection may
not be possible if fingerprints are attached to these areas. If fingers have
inadvertently touched the areas, wipe the areas using a soft, clean cloth.
ZX1-LD300
ZX1-LD600
ZX1-LD50
ZX1-LD100
2-M3
P=0.5
3.2±0.1
49.3±0.1
23.6±0.1
35.3±0.1
4.5±0.1
2-M4
P=0.7
61.5±0.1
30.1±0.1
45.6±0.1
Reference
surface
Mounting hole dimensions (Unit: mm)
Emitter/Receiver direction
Reference
surface
Reference
surface Reference
surface
<Detection Near the Wall Surface>
<Detection of Workpiece with Level Difference>
<Cavity Detection>
Stable detection is possible
regardless of level difference.
Level difference may cause
an abnormal detection value.
The Sensor is less
inuenced by ambient
lighting.
The Sensor is easily inuenced by
ambient lighting, which may cause
detection value variations. *
Detection is not possible if
the emitter or receiver section
is blocked.
■ Caution on Mounting Direction
* Before performing tuning, apply mat paint on the wall surface or turn ON the background suppression
function to avoid laser light reection.
Refer to " 5. Background suppression function,
Detailed Settings"
The following precautions must be observed, since they are essential to ensure safety in operation.
■ Installation Environment
•Do not use the Sensor in locations subject to explosive or ammable gases.
• To ensure safety in operation and maintenance, do not install the Sensor near high-voltage
equipment or power devices.
ON: Laser turns OFF (radiation stop). In this state, analog output, digital
display, judgment output and judgment output display are output based on
keep function settings. The digital display shows [ ].
(2) USA
This product is subjected to the U.S. FDA (Food and
Drug Administration) laser regulations. The ZX1-LD
and ZX1-LDL is already reported to
CDRH (Center for Devices and Radiological Health).
Accession Number:
(ZX1-LD :1210041-000)
(ZX1-LDL :1210041-001)
When using a device equipped with the The ZX1-LD
and The ZX1-LD L in the U.S., attach an FDA
certication label on the sensor at the correct location as
indicated,and replace the warning label or explanatory
label with corresponding English Label(FDA).
The ZX1-LD is classied into Class 2 by the IEC
60825-1:2007 standard according to the regulations of
Laser Notice No.50 of the FDA standard.
The ZX1-LDL is classied into Class 1 by the IEC
60825-1:2007 standard according to the regulations of
Laser Notice No.50 of the FDA standard.
(3) China
The ZX1-LD is classied into Class 2 by the GB7247.1:2012 standard. When using in China,
warning labels must be replaced by Chinese ones supplied with the product.
The ZX1-LDL is classied into Class 1 by the GB7247.1:2012 standard.
(4)Usage in countries other than Japan, U.S. and China
・When usage in countries other than Japan, U.S. and China, warning labels must be replaced by
suitable for the area ones supplied with the ZX1-LD□□. When exporting to Europe, labels fall
under EU standard EN60825-1:2014. The ZX1-LD□□ is classied into Class 2 by the IEC
60825-1:2014 / EN 60825-1:2014 standard.
Do not expose your eyes to the laser radiation either directly
(i.e., after reflection from a mirror or shiny surface). Loss of
sight may possibly occur in case of the exposure to laser
high power density.
Caution - Use of controls or adjustments or performance of
procedures other than those specified herein may result in
hazardous radiation exposure
*0199560-4H*