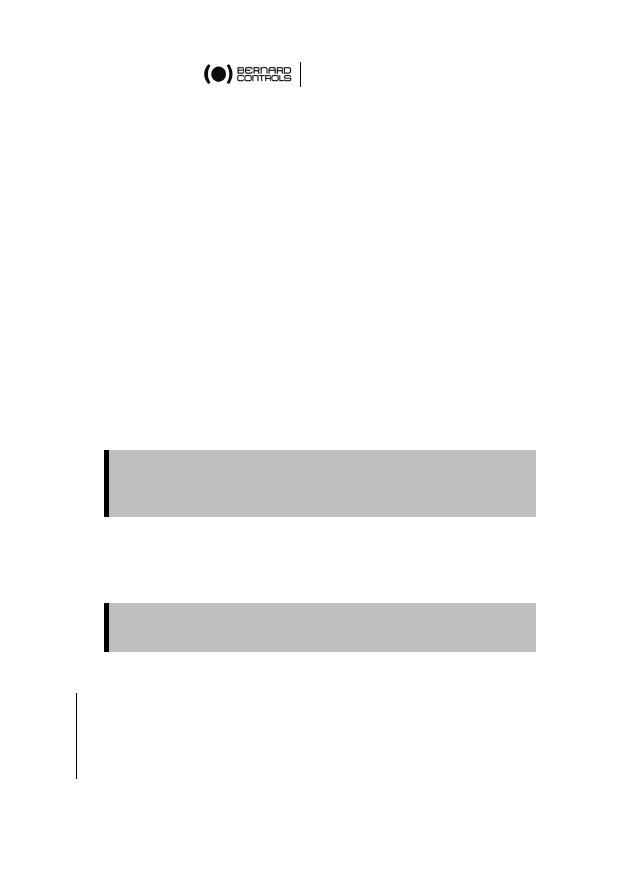
English
1 SAFETY
This device complies with current applicable safety standards.
Installation, maintenance and use of this unit require a skilled and
trained staff.
Please carefully read this whole document before mounting and
starting-up the actuator.
2 PACKAGING, STORAGE AND MAINTENANCE
Packaging
AQ actuators are delivered in a cardboard box of a size equivalent to
the actuator and sit in a cardboard wedge.
Storage
Actuators should be stored under a shelter, in a clean and dry place
and protected from wide temperature variations.
• Avoid placing the actuator directly on the floor.
• Check that plugs on cable entries are correctly tightened.
• Check that cover screws are correctly tightened to ensure
weatherproof sealing of the cover.
AQ actuators include electrical components and lubricated gears.
Even with a weatherproof enclosure, oxidation, seizing and other
alterations may occur if actuators are not correctly stored.
What to check after storage
1. Visually check the electrical equipment.
2. Manually operate micro-switches, buttons, selectors, etc., to
ensure their proper mechanical functioning.
3. Manually operate the actuator.
Heating element should be connected to power supply especially
if the storage place is wet (standard 230 VAC, except
otherwise specified).
4