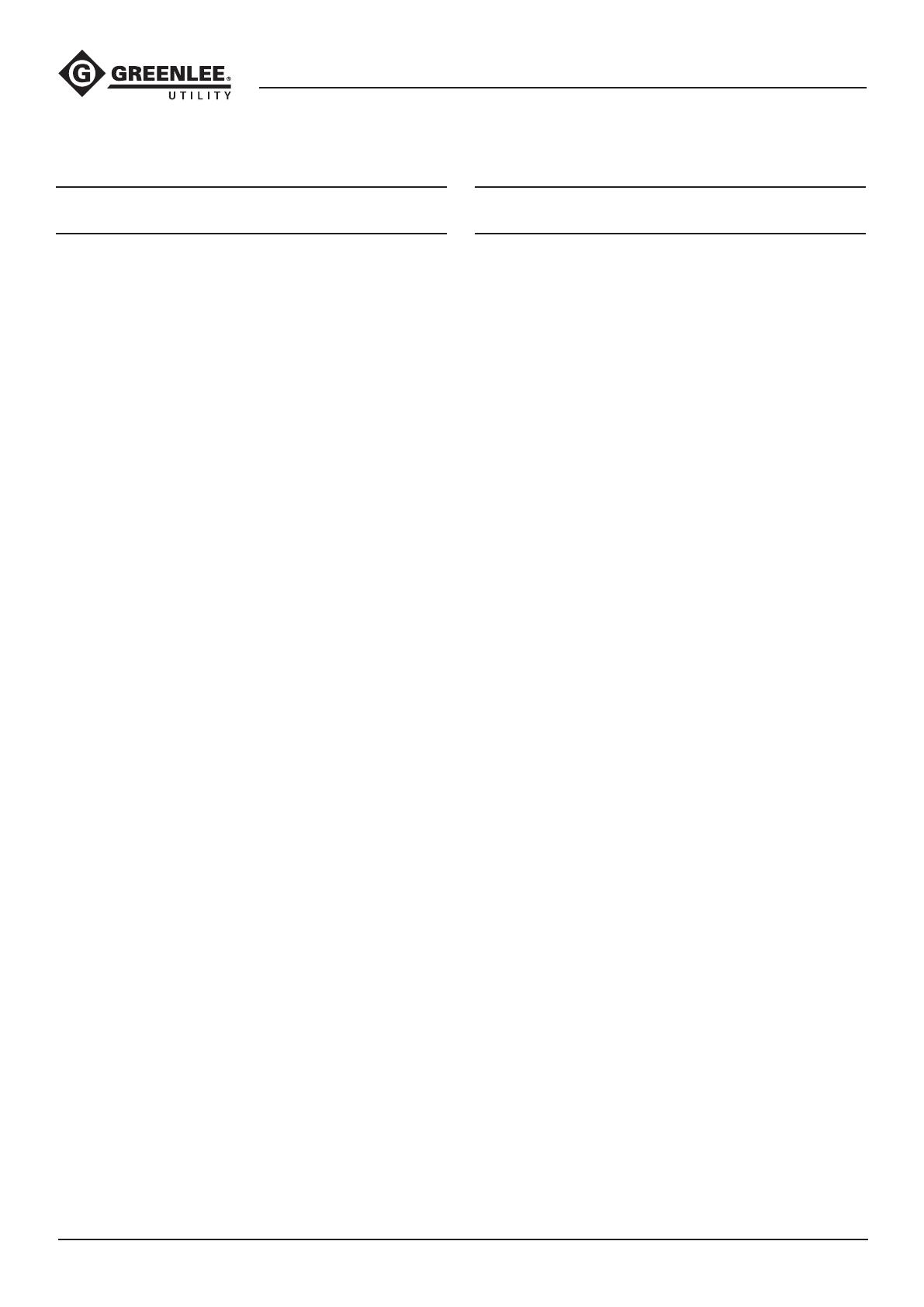
HB10 Dynapress
®
Hydraulic Booster
Greenlee / A Textron Company 4455 Boeing Dr. • Rockford, IL 61109-2988 USA • 815-397-7070
12
Parts List
1 76834 52001736 Housing, wobble plate ............................1
2 20967 52024955 Housing assembly, motor Gerotor ..........1
3 10376 52024956 Housing assembly,
scavenger Gerotor .................................1
4 49834 50498347 Housing, high pressure ...........................1
5 49835 52001738 Screw, cap, 5/16–18 x 4.5, skt hd ..........6
6 13144 52001038 Plate, wobble ..........................................1
7 13131 52001039 Washer, thrust 1.785 I.D. ........................2
8 41892 50418921 Bearing, thrust 1.750 x 2.500 x .078 ......2
†9 Bushing, piston ......................................2
†10 Piston ......................................................2
11 41895 50418951 Washer, thrust, 1.750 x 2.500 x .032 ......2
*†12 O-ring, .375 x .500 x .062–90D ..............2
†13 Ball, .125 diameter, steel ........................4
*†14 Back-up ring, single turn,
.390 x .4 92 x .048 ...................................2
16 43097 50430971 Bearing, needle, .750 x 1.500 .................3
18 49841 52001743 Shaft, drive .............................................1
19 13143 52001037 Retainer, bearing .....................................1
21 43120 50431200 Pin, dowel, .125 x .875 ...........................1
22 43149 50431498 Pin, dowel, .187 x 1 ................................1
*23 Ball, .187 diameter, steel ........................1
24 41888 50418881 Plug, pipe, 1/16 NPTF level seal.............1
*25 O-ring, .750 x .875 x .062–70D ..............1
26 Washer, lock, 5/16 ..................................6
27 40675 50406751 Cap, relief valve ......................................1
28 43961 50439618 Body, valve unloading ............................1
29 43930 50439308 Pintal, valve unloading ............................1
30 40682 50406821 Retainer, spring cup ................................1
31 41874 50418740 Screw, set, #8–32 x .109 hollow skt .......2
*32 Washer, at, .440 x .680 x .060,
copper ....................................................1
33 40692 50406921 Spring, unloading valve ..........................1
34 49960 52001744 Decal .......................................................1
35 Handle ....................................................1
36 Screw, cap #8 –32 x .375,
button head ............................................4
37 41834 50418341 Dust cap .................................................1
†38 Pin, dowel 1/16 x 7/16 ............................2
39 42096 50420961 Coupler, hydraulic ...................................1
*40 O-ring, .812 x 1.062 x .125–85D ............2
41 41344 50413442 Nipple, pipe 1/4 NPTF x 1.37 hex .........1
42 54169 51541690 Coupler, hydraulic ...................................1
43 41432 50414323 Plug, plastic 3/4 –16 ..............................2
44 41873 50418730 Ball, .500 diameter, steel ........................1
45 49234 50492349 Stop, ball ................................................1
*46 Ring, retaining, .687 Truarc .....................1
†47 Washer, at, .250 x .437 x .031,
copper ....................................................2
*48 O-ring, 2.500 x 2.625 x .062–70D ..........2
49 Screw, set, 1/4 –20 x .250 socket
head cup point .......................................1
50 40742 50407422 Pin, dowel, .188 x .500 ...........................6
*51 O-ring, .187 x .312 x .062–90D ..............1
*52 O-ring .....................................................1
53 40696 50406960 Retainer, check valve ..............................1
54 40697 50406970 Body, check valve ...................................1
*55 O-ring, .625 x .812 x .094–90D ..............1
56 41830 50418301 Dust cap .................................................1
Repair Kits
* 49979 50499793 Packing kit (includes items marked
with an asterisk) ......................................1
† 49980 50499807 Piston/bushing assembly (includes
items marked with †) ..............................1
UPC No.
Key 78-3310- Part No. Description Qty
UPC No.
Key 78-3310- Part No. Description Qty