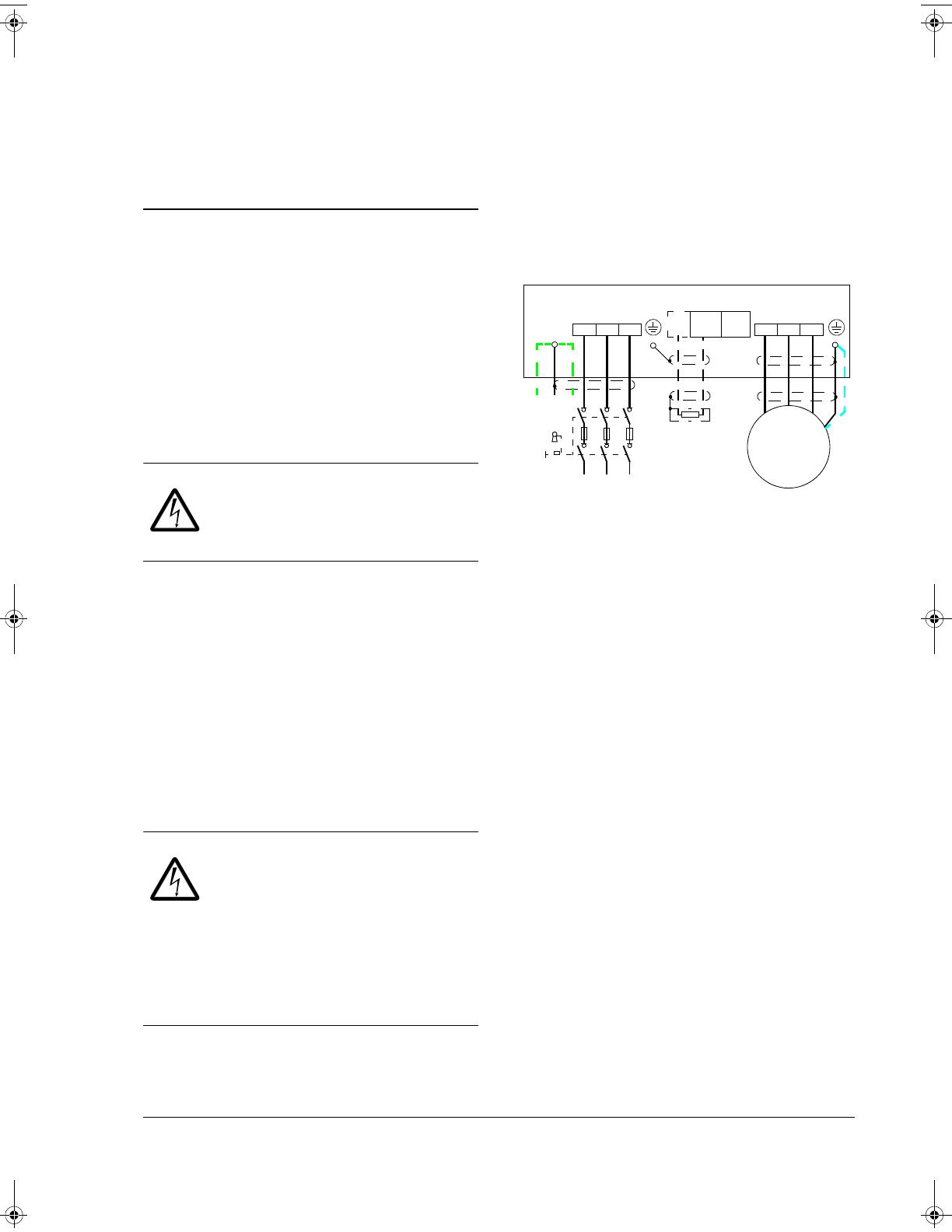
Quick installation guide – ACS850-04
3
Quick installation guide –
ACS850-04
About this guide
This guide contains the very basic information
about the mechanical and electrical installation
of the ACS850-04 drive module (55 to 160 kW).
For complete documentation see ACS850-04
Drive Modules (55…160 kW, 75…200 hp)
Hardware Manual (code: 3AUA0000045487
[English]).
Safety instructions
WARNING! All electrical installation
and maintenance work on the drive
must be carried out by qualified
electricians only.
Never work on the drive, the braking chopper
circuit, the motor cable or the motor when input
power is applied to the drive. Always ensure by
measuring that no voltage is actually present.
A rotating permanent magnet motor can
generate a dangerous voltage. Lock the motor
shaft mechanically before connecting a
permanent magnet motor to the drive, and
before doing any work on a drive system
connected to a permanent magnet motor.
Mechanical installation
WARNING! If the drive is to be
connected to an IT power system
(i.e. ungrounded, or high-resistance-
grounded [over 30 ohms] power
system), the internal EMC filtering of
the drive must be disconnected. This should be
done before the drive is mechanically installed.
Refer to the Hardware Manual for detailed
instructions.
Fasten the drive module onto the wall with four
screws.
Installing the power cables
Connection diagram
Notes:
– Do not use a non-shielded or asymmetrically-
constructed motor cable. It is recommended to
use a shielded cable also as an supply (input)
cable.
– If shielded supply (input) cable is used, and
the conductivity of the shield is less than 50%
of the conductivity of a phase conductor, use a
cable with a ground conductor (1) or a separate
PE cable (2).
– For motor cabling, use a separate ground
cable (3) if the conductivity of the cable shield
is less than 50% of the conductivity of a phase
conductor and the cable has no symmetrical
ground conductors.
If there is a symmetrically-constructed ground
conductor in the motor cable in addition to the
conductive shield, connect it to the ground
connectors at both the drive and motor ends.
INPUT OUTPUT
U1
V1
W1
3
~
Motor
U1
1)
UDC+
R+
UDC
-
R
-
L1 L2 L3
(PE) (PE)PE
2)
3)
PE
Optional
braking resistor
(360°
grounding
required)
ACS850-04
V1 W1 U2 V2 W2
PE
ACS850-04_E0_E_quickguide.book Page 3 Tuesday, February 21, 2012 10:41 AM