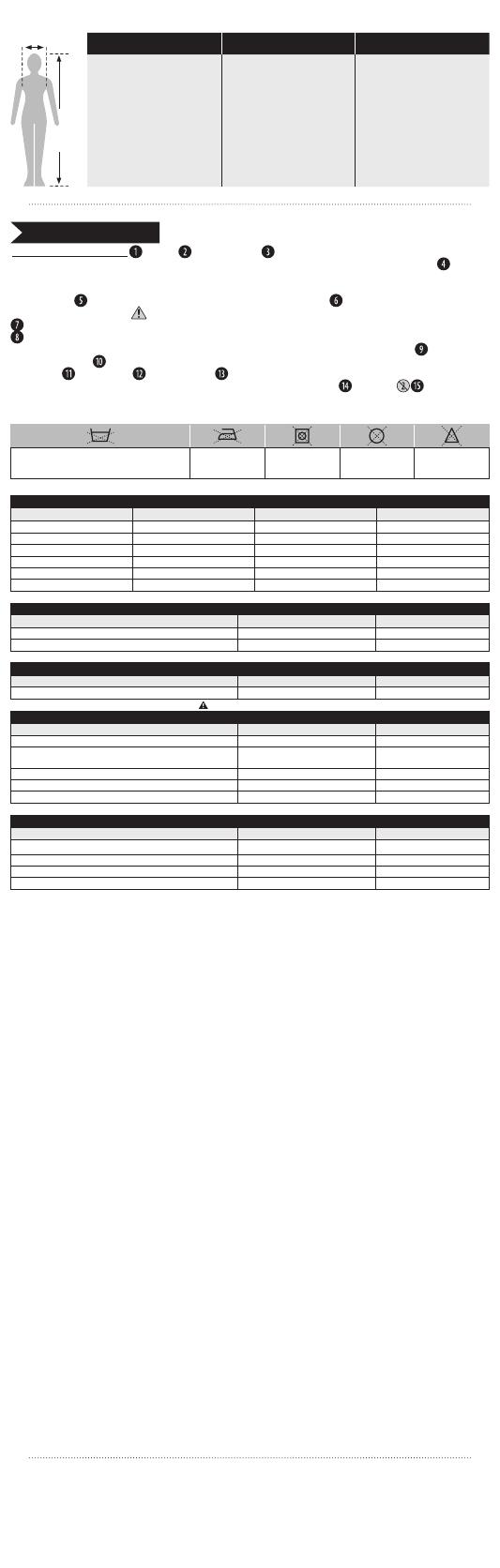
IFU . 2
ENGLISH
INSTRUCTIONS FOR USE
INSIDE LABEL MARKINGS
Trademark. Coverall manufacturer. Model identification - Tyvek® 500 Xpert TY198S LA-B is the model name
for a hooded protective coverall with cuff, ankle, facial and waist elastication. This instruction for use provides information on this coverall. CE marking -
Coverall complies with requirements for category III personal protective equipment according to European legislation, Regulation (EU) 2016/425. Type-
examination and quality assurance certificates were issued by SGS Fimko Oy, Takomotie 8, FI-00380 Helsinki, Finland, identified by the EC Notified
Body number 0598. Indicates compliance with European standards for chemical protective clothing. Protection against particulate radioactive conta-
mination according to EN 1073-2:2002. EN 1073-2 clause 4.2. requires resistance to ignition. However resistance to ignition was not tested on this coverall.
This coverall is antistatically treated and offers electrostatic protection according to EN 1149-1:2006 including EN 1149-5:2018 when properly grounded.
Full-body protection “types” achieved by this coverall defined by the European standards for chemical protective clothing: EN ISO 13982-1:2004 + A1:2010
(Type 5) and EN 13034:2005 + A1:2009 (Type 6). This coverall also fulfills the requirements of EN 14126:2003 Type 5-B and Type 6-B. Wearer should read
these instructions for use. Sizing pictogram indicates body measurements (cm) & correlation to letter code. Check your body measurements and select
the correct size. Country of origin. Date of manufacture. Flammable material. Keep away from fire. This garment and/or fabric are not flame
resistant and should not be used around heat,open flame, sparks or in potentially flammable environments. Do not re-use. Other certification(s)
information independent of the CE marking and the European notified body.
THE FIVE CARE PICTOGRAMS INDICATE
Do not wash. Laundering impacts upon protective
performance (e. g. antistat will be washed off). Do not iron. Do not machine dry. Do not dry clean. Do not bleach.
PERFORMANCE OF THIS COVERALL:
FABRIC PHYSICAL PROPERTIES
Test Test method Result EN Class*
Abrasion resistance EN 530 Method 2 > 100 cycles 2/6***
Flex cracking resistance EN ISO 7854 Method B > 100 000 cycles 6/6***
Trapezoidal tear resistance EN ISO 9073-4 > 10 N 1/6
Tensile strength EN ISO 13934-1 > 60 N 2/6
Puncture resistance EN 863 > 10 N 2/6
Surface resistance at RH 25%** EN 1149-1:2006 • EN 1149-5:2018 inside and outside ≤ 2,5x109 Ohm N/A
N/A = Not applicable *According to EN 14325:2004 **See limitations of use *** Visual end point
FABRIC RESISTANCE TO PENETRATION BY LIQUIDS EN ISO 6530
Chemical Penetration index - EN Class* Repellency index - EN Class*
Sulphuric acid (30%) 3/3 3/3
Sodium hydroxide (10%) 3/3 3/3
* According to EN 14325:2004
FABRIC RESISTANCE TO PERMEATION BY LIQUIDS (EN ISO 6529 METHOD A - BREAKTHROUGH TIME AT 1 g/cm2/min)
Chemical Breakthrough time (min) EN Class*
Sulphuric acid (18%) > 480 6/6
* According to EN 14325:2004 Stitched seams do not offer a barrier to permeation of liquids
FABRIC RESISTANCE TO PENETRATION OF INFECTIVE AGENTS
Test Test method EN Class*
Resistance to penetration by blood and body fluids using synthetic blood ISO 16603 3/6
Resistance to penetration by blood-borne pathogens using
bacteriophage Phi-X174 ISO 16604 Procedure C 2/6
Resistance to penetration by contaminated liquids EN ISO 22610 1/6
Resistance to penetration by biologically contaminated aerosols ISO/DIS 22611 1/3
Resistance to penetration by biologically contaminated dust ISO 22612 1/3
* According to EN 14126:2003
WHOLE SUIT TEST PERFORMANCE
Test method Test result EN Class
Type 5: Particle aerosol inward leakage test (EN ISO 13982-2) Pass*** • Ljnm 82/90≤30% • Ls 8/10≤15% ** N/A
Protection factor according to EN 1073-2 > 50 2 of 3***
Type 6: Low level spray test (EN ISO 17491-4, Method A) Pass N/A
Seam strength (EN ISO 13935-2) > 75 N 3/6*
N/A = Not applicable *According to EN 14325:2004 ** 82/90 means 91,1 % Ljnm values ≤ 30 % and 8/10 means 80 % Ls values ≤15 %
***Test performed with taped cuffs, hood, ankles and zipper flap
For further information about the barrier performance, please contact your supplier or DuPont: dpp.dupont.com
RISKS AGAINST WHICH THE PRODUCT IS DESIGNED TO PROTECT:
This coverall is designed to protect workers from hazardous
substances, or sensitive products and processes from contamination by people. It is typically used, depending on chemical toxicity and exposure conditions,
for protection against fine particles (Type 5) and limited liquid splashes or sprays (Type 6). A full face mask with filter appropriate for the exposure conditions
and tightly connected to the hood and additional taping around the hood, cuffs, ankles and zipper flap are required to achieve the claimed protection. Fabric
used for this coverall has been tested according to EN 14126:2003 (protective clothing against infective agents) with the conclusion that the material offers a
limited barrier against infective agents (see above table).
LIMITATIONS OF USE
: This garment and/or fabric are not flame resistant and should not be used around heat, open flame, sparks or in potentially
flammable environments. Tyvek® melts at 135°C. It is possible that a type of exposure to bio hazards not corresponding to the tightness level of the garment
may lead to a bio-contamination of the user. Exposure to certain very fine particles, intensive liquid sprays and splashes of hazardous substances may require
coveralls of higher mechanical strength and barrier properties than those offered by this coverall. The user must ensure suitable reagent to garment compat-
ibility before use. In addition, the user shall verify the fabric and chemical permeation data for the substance(s) used. Stitched seams of this coverall do not
offer barrier to infective agents nor are a barrier to permeation of liquids. For increased protection the wearer should select a garment comprising seams that
offer equivalent protection as the fabric (e.g. stitched & overtaped seams). For enhanced protection and to achieve the claimed protection in certain applica-
tions, taping of cuffs, ankles, hood and zipper flap will be necessary. The user shall verify that tight taping is possible in case the application would require
doing so. Care shall be taken when applying the tape, that no creases appear in the fabric or tape since those could act as channels. When taping the hood,
small pieces (+/- 10 cm) of tape should be used and overlap. This garment meets the surface resistance requirements of EN 1149-5:2018 when measured
according to EN 1149-1:2006. The antistatic treatment is only effective in a relative humidity of 25% or above and the user shall ensure proper grounding
of both the garment and the wearer. The electrostatic dissipative performance of both the suit and the wearer needs to be continuously achieved in such a
way as the resistance between the person wearing the electrostatic dissipative protective clothing and the earth shall be less than 108 Ohm e.g. by wear-
ing adequate footwear/flooring system, use of a grounding cable, or by any other suitable means. Electrostatic dissipative protective clothing shall not be
opened or removed whilst in presence of flammable or explosive atmospheres or while handling flammable or explosive substances. Electrostatic dissipative
protective clothing is intended to be worn in Zones 1, 2, 20, 21 and 22 (see EN 60079-10-1 [7] and EN 60079-10-2 [8]) in which the minimum ignition energy
of any explosive atmosphere is not less than 0.016 mJ. Electrostatic dissipative protective clothing shall not be used in oxygen enriched atmospheres, or in
Zone 0 (see EN 60079-10-1 [7]) without prior approval of the responsible safety engineer. The electrostatic dissipative performance of the electrostatic dis-
sipative clothing can be affected by relative humidity, wear and tear, possible contamination and ageing. Electrostatic dissipative protective clothing shall
permanently cover all non-complying materials during normal use (including bending and movements). In situations where static dissipation level is a criti-
cal performance property, endusers should evaluate the performance of their entire ensemble as worn including outer garments, inner garments, footwear
and other PPE. Further information on grounding can be provided by DuPont. Please ensure that you have chosen the garment suitable for your job. For
advice, please contact your supplier or DuPont. The user shall perform a risk analysis upon which he shall base his choice of PPE. He shall be the sole judge
for the correct combination of full body protective coverall and ancillary equipment (gloves, boots, respiratory protective equipment etc.) and for how long
this coverall can be worn on a specific job with respect to its protective performance, wear comfort or heat stress. DuPont shall not accept any responsibility
whatsoever for improper use of this coverall.
PREPARING FOR USE
: In the unlikely event of defects, do not wear the coverall.
STORAGE AND TRANSPORT
: This coverall may be stored between 15 and 25°C in the dark (cardboard box) with no UV light exposure. DuPont
has performed naturally and accelerated ageing tests with the conclusion that this fabric retains adequate physical strength and barrier properties over a
period of 10 years. The antistatic properties may reduce over time. The user must ensure the dissipative performance is sufficient for the application. Product
shall be transported and stored in its original packaging.
DISPOSAL
: This coverall can be incinerated or buried in a controlled landfill without harming the environment. Disposal of contaminated garments is
regulated by national or local laws.
DECLARATION OF CONFORMITY
: Declaration of conformity can be downloaded at: www.safespec.dupont.co.uk
BODY MEASUREMENTS CM
Size Chest girth Body height
SM 84 - 92 162 - 170
MD 92 - 100 168 - 176
LG 100 - 108 174 - 182
XL 108 - 116 180 - 188
2XL 116 - 124 186 - 194
3XL 124 - 132 192 - 200
Body
height
Chest girth